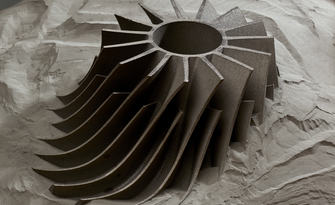
Si è svolta nel nuovo Advanced Laser Center di Prima Industrie la seconda edizione degli Innovation Days, l’evento internazionale dedicato alle tecnologie innovative per l’Additive Manufacturing e la lavorazione della lamiera, a cui hanno partecipato oltre 300 ospiti, tra i quali clienti, università e centri di ricerca, stampa di settore italiana.
Durante gli Innovation Days 2019 sono stati presentati i sistemi di nuova generazione per la produzione additiva di componenti in metallo di Prima Additive. Le novità mostrate durante l’evento coprono entrambe le tecnologie AM: Powder Bed Fusion (PBF) e Direct Energy Deposition (DED).
I nuovi sistemi sono stati progettati seguendo l’approccio Open Innovation del gruppo, che pone al centro le esigenze e le applicazioni dei clienti, garantendo una stretta partnership con gli utenti finali delle tecnologie e una forte aderenza alle richieste del mercato.
Altra leva importante nei progetti di innovazione del gruppo è la sostenibilità. Seguendo la sua vocazione “green”, Prima Industrie ha sviluppato prodotti ad alta efficienza energetica che riducono i consumi rispetto ai sistemi tradizionali e garantiscono elevate prestazioni. I prodotti Prima Additive permettono inoltre di abbracciare il paradigma di business della Circular Economy, che mira a mantenere il valore di prodotti e materiali il più a lungo possibile, trasformando le risorse alla fine del loro ciclo di vita in nuovi input nel processo di creazione del valore.
Molte aziende di diversi settori industriali stanno adottando le tecnologie di additive manufacturing per la loro produzione, anche per soddisfare le sempre maggiori richieste di customizzazione dei prodotti da parte del mercato. Prima Industrie risponde a queste esigenze con prodotti che permettono di sfruttare tutti i vantaggi competitivi dell’Additive Manufacturing, grazie all’alta produttività, all’affidabilità di processo di prim’ordine, all’eccellente qualità dei pezzi finiti e all’ottimo rapporto prestazioni-prezzo.
Agli Innovation Days Prima Industrie ha presentato la Print Genius 250, la nuova macchina PBF con volume di costruzione di 262x262x350 mm, adatta alla produzione di componenti di media dimensione. Print Genius 250 è la soluzione ideale per applicazioni di stampa di metallo ad alta produttività grazie al suo doppio laser single-mode da 500 W, che riduce i tempi di produzione, abbinato a software intelligenti per un rapido orientamento dei pezzi e per la definizione dei parametri macchina
Il flusso di gas ottimizzato con conseguente riduzione al minimo dei consumi e la capacità di cambio completo del materiale in meno di 2 ore sono altri punti di forza di questa macchina innovativa. Print Genius 250 è dotata di un’unità filtrante a doppia linea per il ricircolo del gas all’interno dell’area di lavoro, che mantiene un elevato grado di pulizia della macchina e riduce al minimo la sostituzione delle parti soggette ad usura. Il nuovo HMI consente di monitorare in tempo reale l’ambiente di costruzione e di generare report con tutti i principali parametri di stampa tracciabili.
La Print Genius 250 è adatta a una vasta gamma di materiali: acciaio inossidabile, acciaio Maraging, leghe a base di nichel ad alta temperatura (Inconel), titanio, cobalto-cromo, alluminio, rame e acciaio alto-resistenziale.
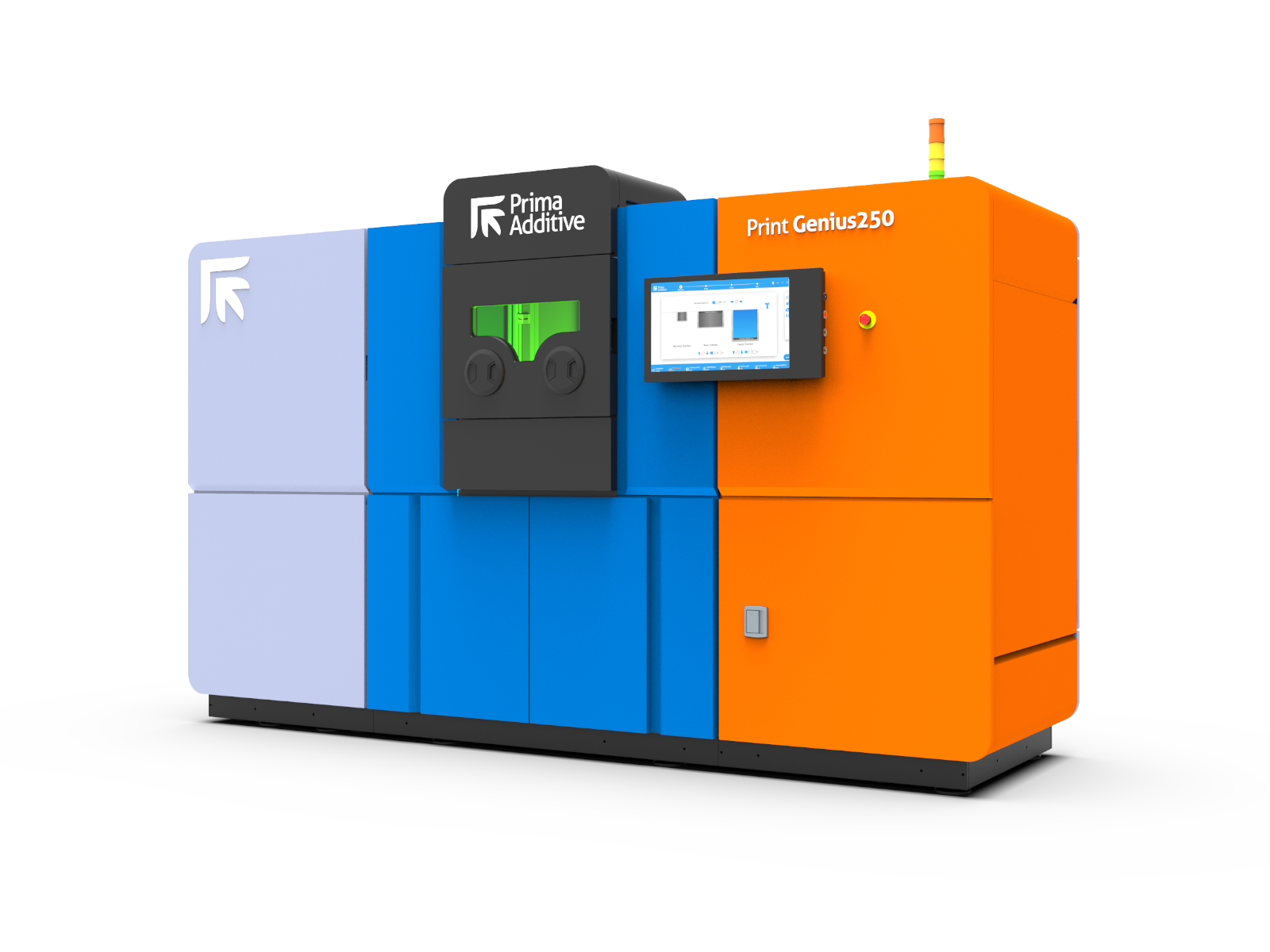
Nell’ambito della tecnologia Direct Energy Deposition, agli Innovation Days è stata presentata la nuova Laserdyne 430 DED, una macchina compatta e precisa a 3 assi con volume di lavoro di 585x400x500 mm, elevata velocità di costruzione (max 40-50 cm3 /h – tipico 20 cm3
/h) ed eccellente qualità dei pezzi finiti, adatta per produzioni 3D, rilavorazioni e riparazioni.
La Laserdyne 430 DED è dotata di Advanced Head, l’innovativa testa laser DED multiuso con design modulare che consente il montaggio in diverse configurazioni per adattarsi a molteplici processi laser. Alcuni dei punti di forza della nuova testa sono: il monitoraggio del pool di fusione, il percorso ottico pressurizzato che evita infiltrazioni di polvere, e l’ugello raffreddato ad acqua per deposizione continua realizzato in additive, che riduce il rischio di adesione della polvere durante il processo. La testa offre inoltre una facile manutenzione e un veloce allineamento dello spot polvere / laser.
La Advanced Head può essere montata su tutti i prodotti Laser Metal Deposition di Prima Industrie, ed è anche disponibile come parte del Laser Metal Deposition Kit di Prima Additive, che include la testa, una sorgente laser ad alta efficienza, un alimentatore di polvere flessibile e un software CAM per la programmazione off-line. Il Kit può essere integrato in qualsiasi macchinario e sistema robotico.
La flessibilità della Laserdyne 430 DED può essere ulteriormente incrementata grazie all’aggiunta di una tavola roto-basculante opzionale, che aggiunge altri due assi per applicazioni più complesse.
I 4000 m2 dell’Advanced Laser Center sono dedicati al nuovo laboratorio di ricerca e innovazione dei sistemi di produzione laser avanzati. L’edificio è stato costruito con i più recenti criteri di edilizia sostenibile e sfrutta sistemi geotermici e pannelli solari per ridurre al minimo l’impatto ambientale.
La nuova sede fa parte di un programma più ampio di rinnovamento dei siti del gruppo, iniziata nel 2016 con la realizzazione del nuovo Headquarters e Tech Center di Collegno, che si completerà entro il prossimo anno con la costruzione del nuovo stabilimento produttivo per le macchine laser, attualmente situato in un’altra area della città. L’investimento complessivo sul territorio è di circa 25 milioni di euro e permetterà a Prima Industrie di aumentare l’efficienza, accorpando le sedi di Collegno, migliorare la customer experience nelle aree dedicate ai visitatori e di poter contare su ambienti lavorativi più moderni e organizzati.
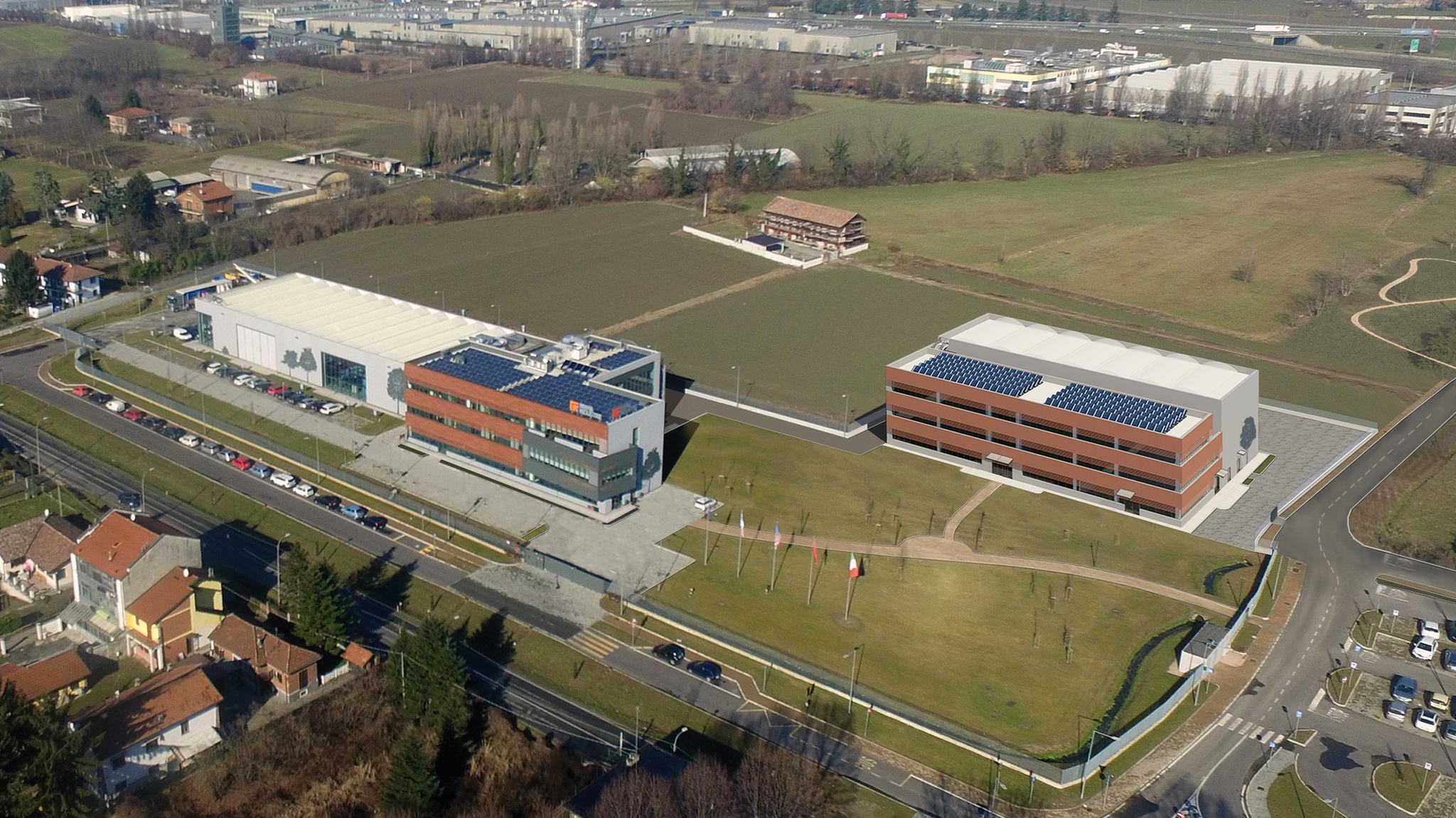