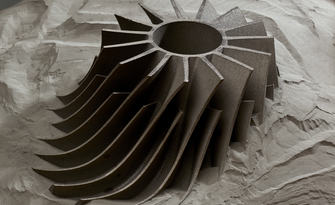
Additive manufacturing for the Aerospace industry
Additive manufacturing is not only part of the future, but also of the present in the aerospace sector. The need to make lighter parts, with higher quality mechanical properties while using more efficient materials is a perfect match for additive technologies.
Learn about all the innovations of additive manufacturing for the aerospace industry and ask us for advice now.
PRIMA ADDITIVE FOR AEROSPACE
Find out what we do for the aerospace sector
Prima Additive’s solutions are pivotal in driving sustainability and efficiency within the aerospace sector. Our advanced manufacturing technologies, such as Powder Bed Fusion and Direct Energy Deposition, enable the production of lighter aircraft components. These components significantly reduce the overall weight of the aircraft, which in turn lowers fuel consumption and decreases CO2 emissions. This not only promotes environmental stewardship but also aligns with global sustainability goals.
For example, our Direct Energy Deposition technology has been instrumental in developing lightweight yet robust satellite launcher components. These parts are designed with optimized internal structures to enhance airflow and efficiency, thereby reducing the weight and optimizing performances. Similarly, our Powder Bed Fusion process has allowed for the creation of complex geometric components that traditional methods could not achieve, such as lightweight lattice structures for airframe assemblies, which further contribute to fuel efficiency.
In the realm of space exploration, Prima Additive is at the forefront of cost-effective production methods for satellites and launch vehicles. By utilizing our customized metal 3D printing solutions, we can produce highly specialized parts that significantly reduce the cost and complexity of spacecraft manufacturing. This democratizes access to space technology, broadening participation in the global space economy and facilitating more frequent and diverse missions.
Moreover, in the aerospace industry where reliability and performance are crucial, Prima Additive excels by producing parts with unmatched mechanical properties and precise dimensional accuracy. Our processes leverage cutting-edge materials like aerospace-grade titanium and aluminum, renowned for their strength-to-weight ratios and durability. These materials ensure that each component not only meets but exceeds industry standards for performance and reliability.
Our commitment to innovation and quality is exemplified by our ongoing research into novel additive manufacturing materials and techniques. This includes the development of high-temperature alloys capable of withstanding the extreme environments of aerospace applications, which further enhances the operational capabilities and lifespan of aerospace components.
Design Freedom and Complexity
Additive manufacturing (AM) enables the creation of complex geometries and intricate designs that are difficult or impossible to achieve with traditional manufacturing methods. This allows for the production of lightweight, structurally optimized aerospace components with enhanced performance characteristics, contributing to significant improvements in fuel efficiency and overall aircraft performance.
Cost Efficiency and Material Savings
AM processes, such as Directed Energy Deposition (DED) and Powder Bed Fusion (PBF), build components layer by layer, which significantly reduces material waste compared to subtractive manufacturing methods. This not only lowers the cost of raw materials but also contributes to more sustainable manufacturing practices. Additionally, the ability to produce components directly from digital models can reduce lead times and inventory costs.
Improved Sustainability and Environmental Impact
The aerospace sector benefits from AM's ability to produce lighter components that directly contribute to improved fuel efficiency and reduced CO2 emissions during flight. By optimizing part designs for weight reduction without compromising strength or safety, AM plays a crucial role in the aerospace industry's efforts to minimize its environmental footprint.
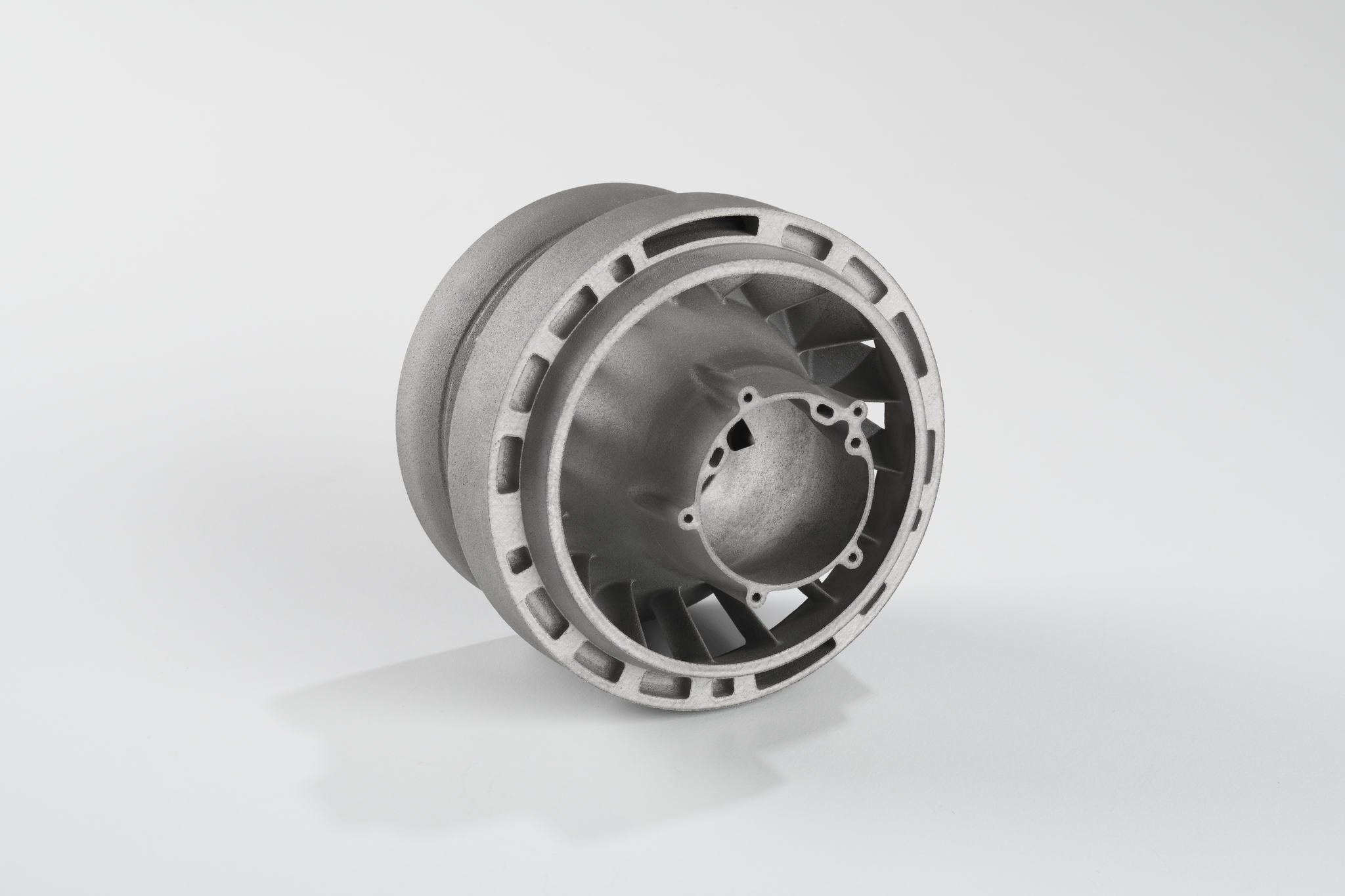
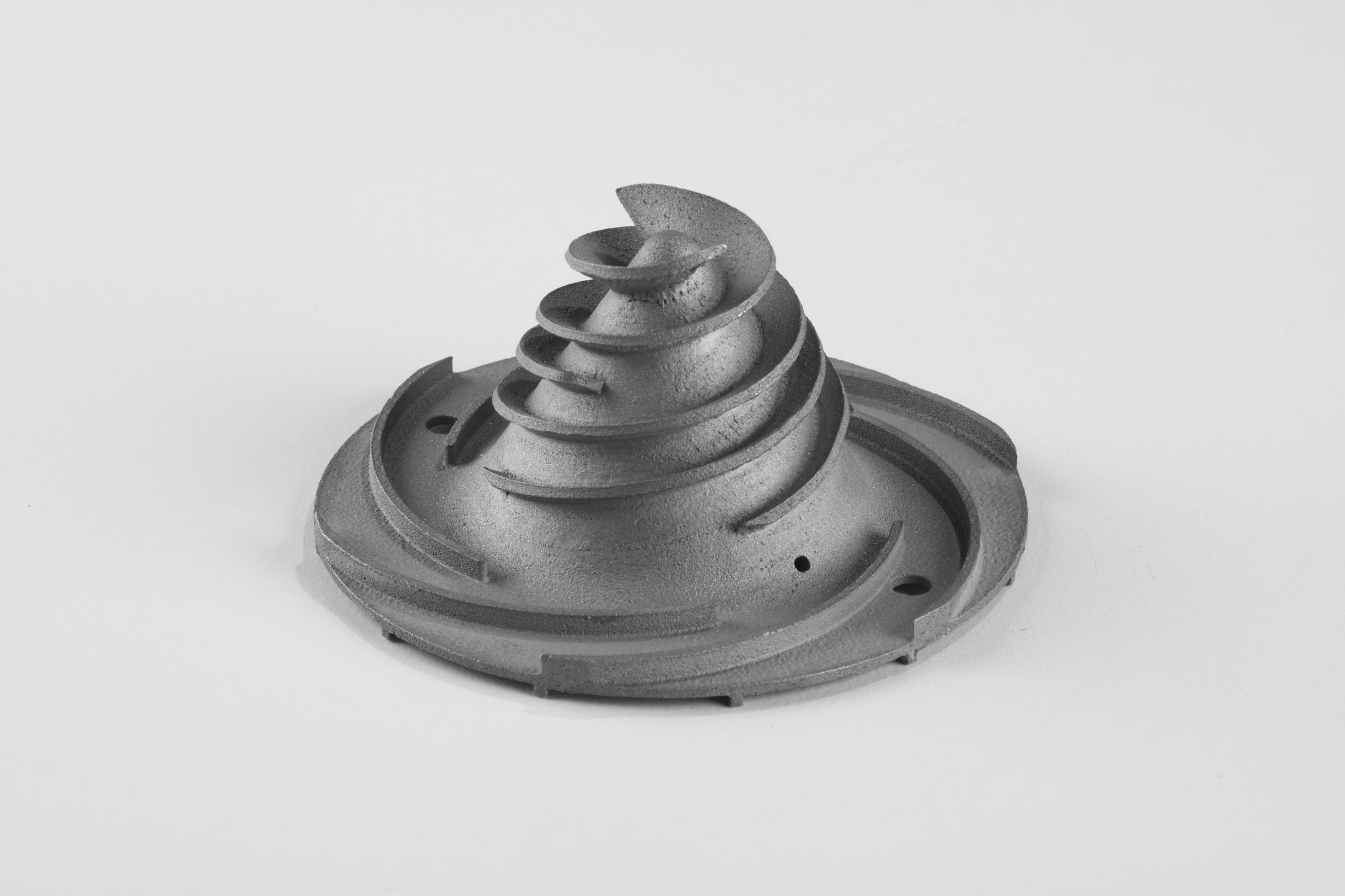
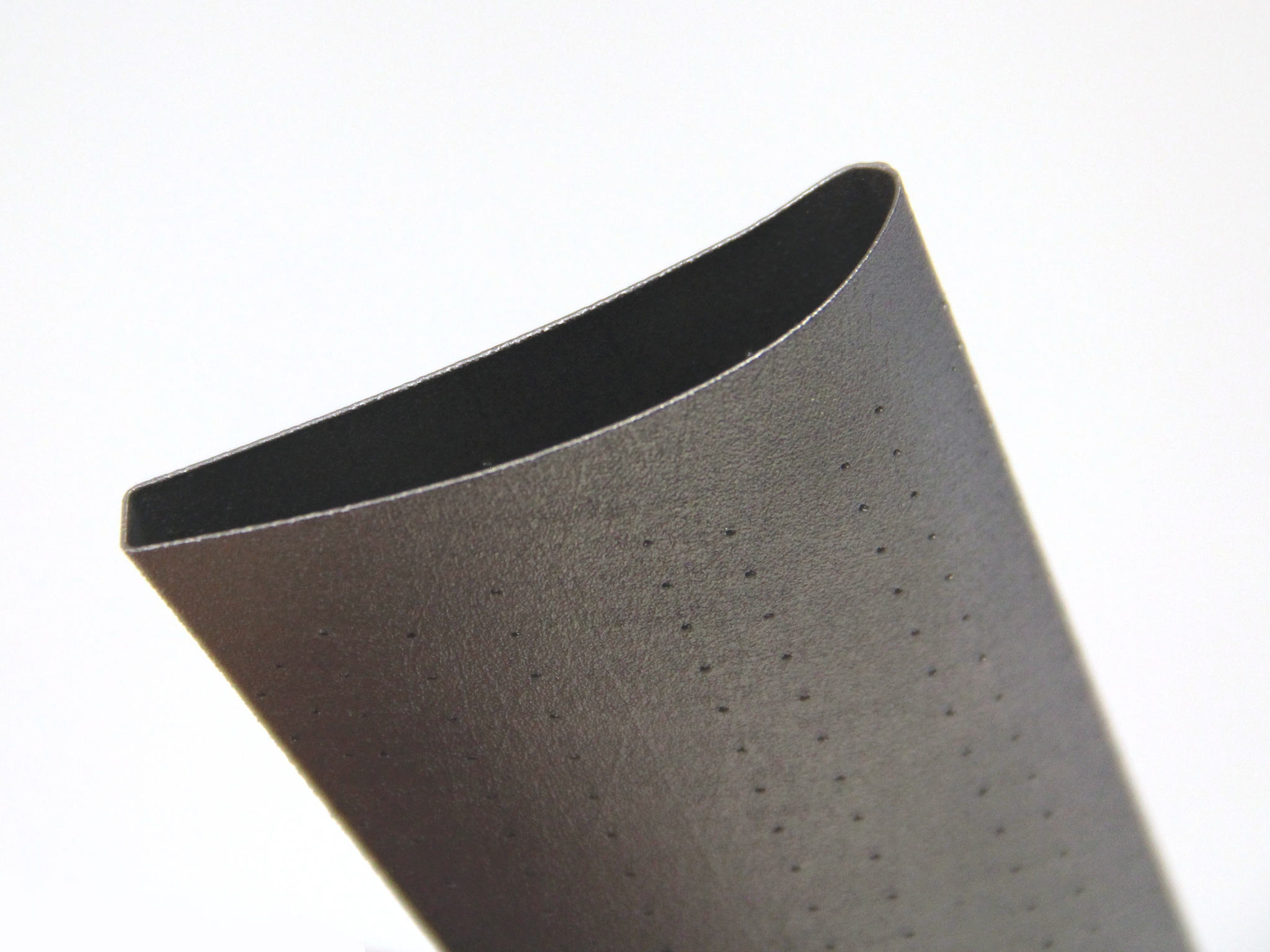
SOLUTIONS
Find your ideal solution
Especially in the aerospace sector, it is essential to comply with stringent industry standards, above all NADCAP certification (National Aerospace and Defense Contractors Accreditation Program).
Prima Additive can support you through the entire certification process, including process verification, powder verification and finished product testing, to enable you to obtain certification and produce additive parts using a standardized, repeatable and qualified process.
We are at your service to help you take full advantage of the shape flexibility made possible through metal additive manufacturing.
Main Applications of Metal Additive Manufacturing in the Aerospace Sector
Behind every innovation there is a Prima Additive machine
- Engine Components: The production of complex engine parts, such as fuel nozzles, turbine blades, and heat exchangers, benefits from AM's capability to create lightweight, high-strength structures with improved thermal properties.
- Structural Components: AM is used to manufacture critical structural aircraft components, including brackets, frames, and fuselage parts, which are designed for strength and weight optimization
- Prototyping: Rapid prototyping of aerospace components allows for faster iteration and testing, significantly reducing the development time for new aircraft designs and modifications.
- Customized Parts and Tooling: AM enables the production of customized parts and tooling for specific applications, including jigs, fixtures, and molds, with reduced lead times and costs.
- Repair and Maintenance: Directed Energy Deposition (DED) and other AM processes are employed for the repair of high-value components, extending their service life and reducing maintenance costs.
- Spacecraft Components: The manufacturing of parts for spacecraft and satellites benefits from AM's ability to produce lightweight components that withstand the extreme conditions of space missions.
- Interior Cabin Parts: Additive manufacturing is used to create customized interior cabin components, such as seat frames and ventilation system parts, optimizing for comfort and efficiency.
By leveraging the unique advantages of metal additive manufacturing, the aerospace sector is able to achieve unprecedented levels of performance, efficiency, and innovation in the design and production of aircraft and spacecraft components.
Choose the best material for your application