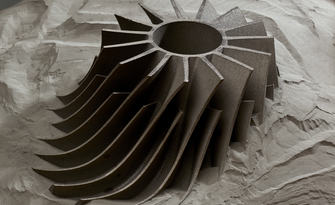
What is powder bed fusion?
Powder Bed Fusion is an additive manufacturing technology commonly used in metal 3D printing. It is also known as laser metal fusion or selective laser melting and it's a category of additive manufacturing processes involving selectively melting a powdered material to create a component layer by layer.
In Powder Bed Fusion, the process begins with a thin layer of powder material evenly distributed on a building platform. A high-energy heat source, that in Prima Additive processes is always a laser, is then used to selectively melt the powder particles according to the pattern based on the 3D model of the object being produced.
The laser beam is precisely controlled to melt the powdered material, causing it to fuse together and solidify. Once a layer is completed, a new layer of fresh powder is spread on top, and the process is repeated until the entire object is built.
Laser Powder Bed Fusion (LPBF) technology is also known as selective laser melting. In selective laser melting, the laser beam raises the temperature of the powder above its melting point, causing the material to completely melt and solidify.
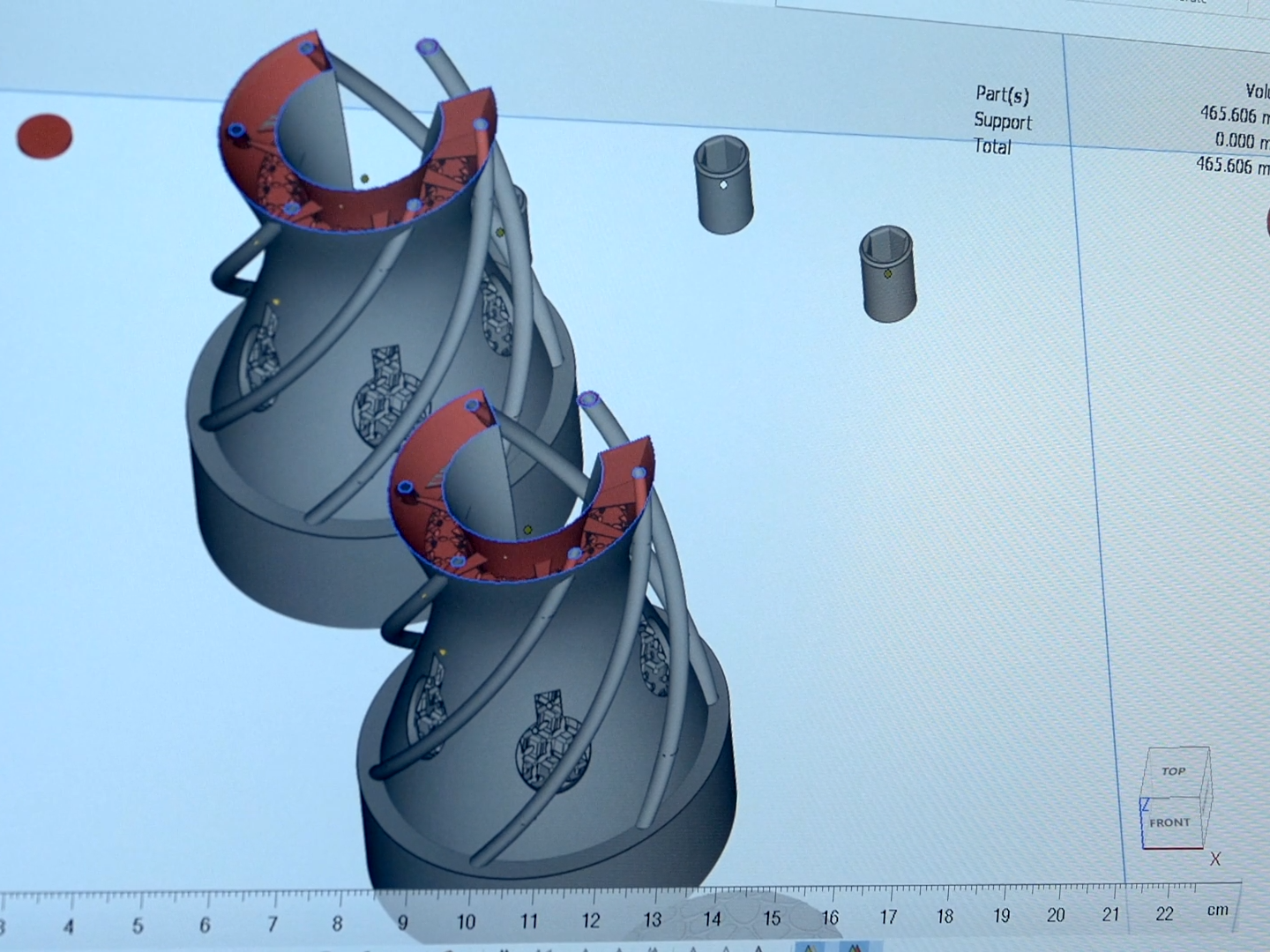
What are the advantages of Laser Powder Bed Fusion technology?
Probably the main advantage of PBF technology is the ability to create complex geometries with high precision and accuracy. But it has also a wide range of benefits, including:
- Design Freedom: powder bed fusion allows designers to have more freedom to create customized and highly optimized parts. The technology eliminates many of the constraints associated with traditional manufacturing methods, enabling the production of unique and tailored designs for specific applications.
- Prototyping and Rapid Iteration: this kind of manufacturing process is also well-suited for rapid prototyping and iterative design processes. It allows for quick and cost-effective production of functional prototypes, enabling designers to test and validate their concepts before committing to large-scale production.
- Material Versatility: powder bed fusion can work with a wide range of materials. Specifically, Prima Additive solutions are well suited to the processing of metal powders of the following alloys: steel, aluminum, nickel, titanium, cobalt-chrome, copper, gold, or other precious metals. Prima Additive also provides material consultancy, helping you find the right metal powders for your application.
- Reduced Waste: this additive process selectively uses only the required amount of material for each part. This leads to minimal raw material waste compared to traditional subtractive methods, with the ability to instantly reuse unused metal in the process.
- Production Efficiency: powder bed fusion can be highly efficient for small to medium production runs, especially for complex parts. The ability to consolidate multiple components into a single, integrated design reduces assembly requirements and simplifies supply chains, leading to potential cost savings and faster time-to-market.
- Improved Performance: Prima Additive solutions can produce metal parts with excellent mechanical properties, as the layer-by-layer fusion process allows for precise control over material microstructure. This results in parts with high strength, enhanced durability, and improved performance characteristics.
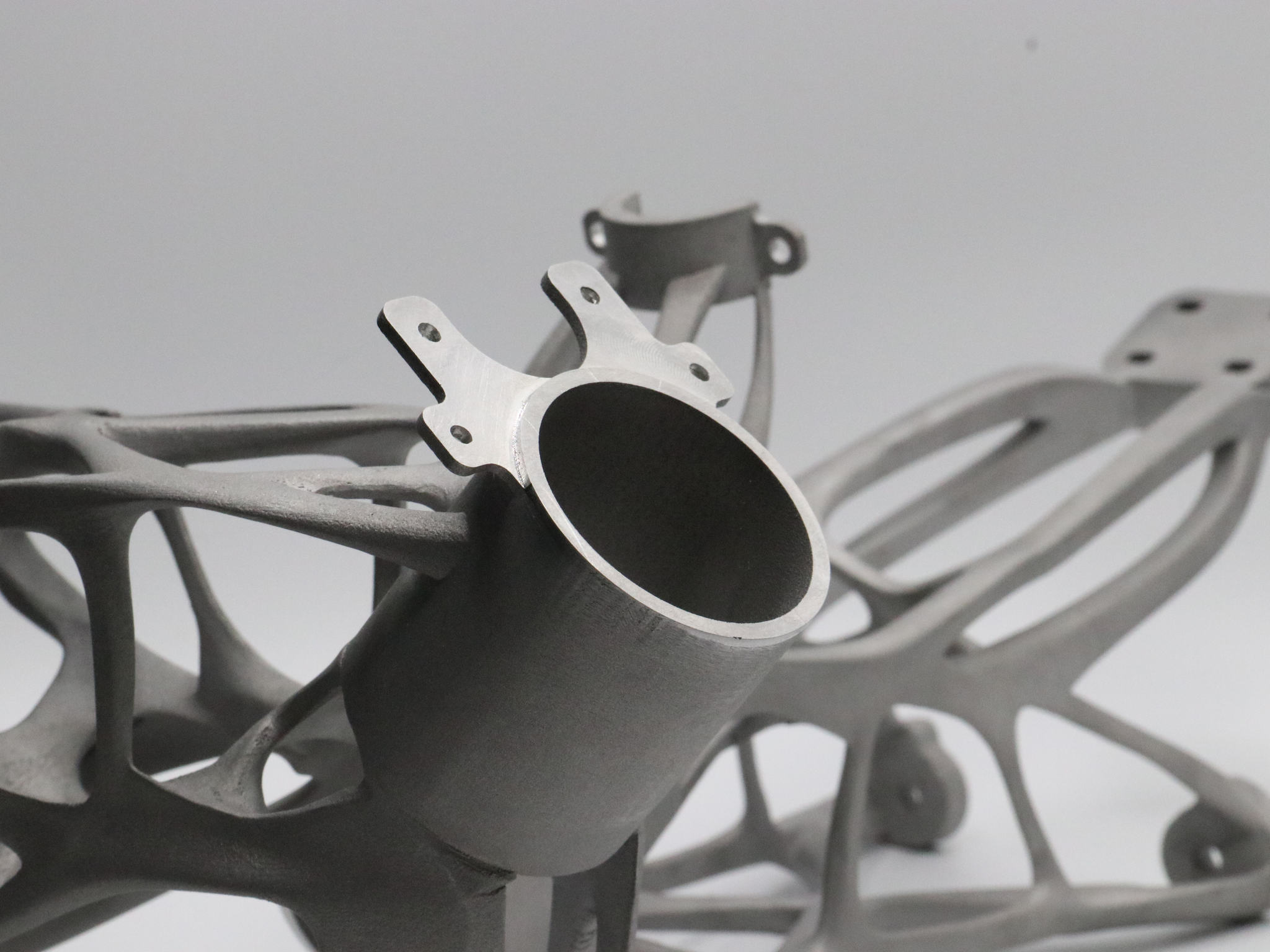
What are the benefits of designing for Powder Bed Fusion?
Designing specifically for powder bed fusion in additive manufacturing can unlock additional benefits for the designers and can highly optimize the production process.
First, we must consider that with selective laser melting we can produce part with complex geometries that are difficult, or even impossible, to achieve with traditional manufacturing methods. By designing specifically for this type of production process, all the possibilities offered can be fully exploited, creating optimized designs. The workshop of the future is the one that does not replace traditional technologies with additive ones, but puts them side by side: based on the post-processing needs, it is therefore possible to design additive components taking into consideration the processing needs next to get the best.
Besides, powder bed fusion enables the consolidation of multiple parts or components into a single, integrated design, reducing the need of assembly, joining, or fastening processes, leading to reduced material usage, weight reduction, improved structural integrity and cost savings.
Another advantage that we like to highlight in Prima Additive is the high level of customization and personalization that we can offer to our customers. In fact, we provide tailor-made solutions for the needs of the end user, recommending the best machine configuration depending on the material to be processed. The choice of materials proves to be crucial in this process: one of the main activities we offer our customers is precisely the identification of the best material for each specific application. Often the required mechanical characteristics can be achieved using more performing materials: for this reason, our experts are always ready to develop the process parameters to open up to new materials enabling further advantages.
Functional features can also be easily included directly in the design of a part produced using powder bed fusion technology. For example, we can design complex internal cooling channels in metal parts for thermal management or providing embedded sensors or electronics.
Prima Additive supports those who want to approach this technology for the first time in understanding how to get the best out of LPBF by providing comprehensive application support. What we do is try to understand the customer's needs, helping them understand how to improve their production by adding metal additive manufacturing to traditional technologies or 3D polymer printing: we do this by providing application studies on the redesign of components, on materials to use, on the choice of technology and so on.
By taking advantage of the unique possibilities offered by Powder Bed Fusion with Prima Additive, the full potential of additive manufacturing design can be unlocked: enabling highly innovative designs and improving performance, customization, and streamlined manufacturing processes.
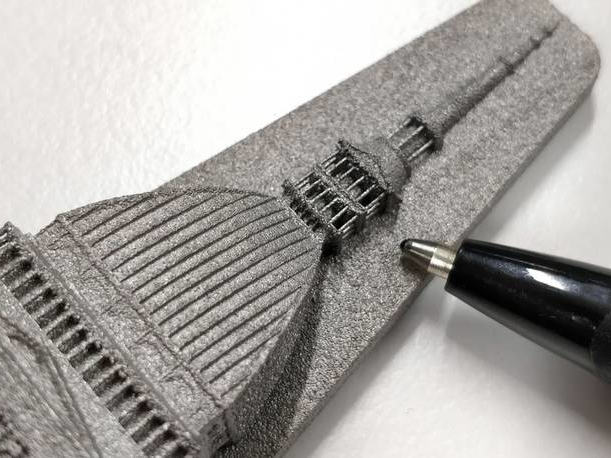