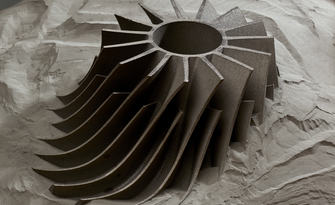
Laser Additive Manufacturing: Revolutionizing Die and Mold Production
The intricacies of mold and die production, essential for various manufacturing processes like injection molding and die casting, are rooted in the necessity for precision and durability. Molds and dies must possess exceptional mechanical characteristics, ensuring longevity and performance under intense operational conditions. The dimensions and complex geometries required are exacting, with little margin for error. This precision is crucial in defining the quality and functionality of the final product, whether it be intricate plastic components produced via injection molding or robust metal parts formed through die casting.
In this landscape, laser-based additive manufacturing technologies, notably Powder Bed Fusion and Direct Energy Deposition, have emerged as transformative tools. These advanced methods offer a myriad of benefits, addressing the conventional challenges faced in mold and die production.

Powder Bed Fusion, a widely recognized technology for creating mold inserts, is known for its ability to fabricate components with complex designs layer by layer from metallic powder. This technology enables the rapid creation of customized molds or mold inserts, significantly enhancing production flexibility.
Similarly, Directed Energy Deposition, also known as Laser Metal Deposition, has shown its effectiveness in adding features to existing components or repairing and modifying large molds. It achieves this by depositing metallic powder through nozzles and fusing it with a laser source, allowing the addition of material where needed. This versatility extends to coating molds with different materials to improve performance, such as enhancing hardness for molds made from materials prone to wear.
In summary, the utilization of laser additive manufacturing technologies like Powder Bed Fusion and Direct Energy Deposition in mold and die production represents a significant advancement. It introduces new levels of design freedom, production efficiency, and customization, which are paramount in today's dynamic manufacturing landscape. The integration of these technologies not only streamlines the mold-making process but also enhances the overall production capability, meeting the evolving demands of industries reliant on precision molding techniques.

Advancing Tooling Efficiency: Prima Additive's Laser Technology Innovations
Prima Additive's commitment to advancing its services and machinery is deeply rooted in its attention to research and technological innovations. The company's focus on enhancing tooling applications for diverse industries through Metal Additive Manufacturing is a prime example of this dedication.
One of the areas in which our research has focused most is the creation of fully dense tool inserts and dies made of high-alloy tool steel. Applications of this type are critical for tooling not only for low-impact processes such as plastic injection molding, but also for more demanding tasks such as metal forming and die casting. The introduction of innovative cooling systems in metalworking molds, through additively manufactured inserts, represents a significant breakthrough. This innovation allows the cooling of specific areas of the mold by placing the cooling channels very close to the mold cavity. These advances aim for shorter cycle times, improvements in the structural and dimensional quality of manufactured parts, and reduced energy consumption.
In the realm of press hardening, the application of laser beam melted tooling inserts has been explored within the "Green Carbody Technologies" innovation alliance. This project aimed to enhance resource efficiency in the hot sheet metal forming process. By developing tool inserts with new types of cooling systems, the project successfully enhanced mechanical properties of hot-formed metal sheets, reduced wall thickness, and decreased energy usage per component during manufacturing.
Moreover, additive manufacturing played a pivotal role in optimizing the die casting processes. The implementation of conformal cooling systems, created using individual laser beam melted tool inserts, marked a significant advancement. Numerical simulation and careful design of the cooling system, including the layout and contour of channels, were crucial in achieving an optimal temperature distribution and reducing critical issues like porosity in the die casting process. The results from these applications in series production have shown a reduction in scrap rates and cycle times, proving the effectiveness and efficiency of these advanced manufacturing techniques.

Elevating Mold Manufacturing with Prima Additive's Advanced Solutions
Also examining studies and scientific articles of this type, Prima Additive, a pioneer in the additive manufacturing industry, has developed a comprehensive suite of laser technologies and support services tailored to the mold manufacturing sector. The company's expertise encompasses two primary laser technologies: Powder Bed Fusion and Direct Energy Deposition. As we said before, these technologies are instrumental in producing complex, custom-designed molds and mold inserts.
Despite the increasing adoption of additive technologies, there are still challenges to be addressed before they become a widely accepted operating methodology among mold manufacturers. The main obstacle probably lies in the lack of familiarity with the technology and the apprehension of end users about the full use of this production method. Traditionally, mold manufacturers have relied on conventional technologies and may feel that they are not able to use and insert into their production context a technology that operates on different design logics.
To overcome these challenges, Prima Additive focuses on lowering the barriers to entry into laser-based metal additive manufacturing. The company provides comprehensive 360-degree application support, starting with analyzing the feasibility, cost-effectiveness, and potential design optimizations of current mold designs. Additionally, Prima Additive offers a digital platform, "Prima Additive Marketplace", where users can upload 3D files of their components and request application studies or direct printing. This initiative enables access to additive technology even without owning a machine, thus catering to businesses with small batch needs or limited investment capabilities.
Prima Additive's laser technologies offer numerous advantages for mold manufacturers. Although molds created using additive manufacturing may initially cost more than those made with traditional methods, the broader view of the process reveals significant benefits. Additive manufacturing systems do not require setup equipment, allowing for the rapid transition from design to finished mold. Moreover, the implementation of conformal cooling channels results in more efficient mold cooling, leading to reduced cycle times, improved final component quality, and lower production waste. This efficiency not only compensates for the initial higher mold cost but also contributes to greater environmental sustainability due to better raw material utilization. Additionally, the Direct Energy Deposition technology enables mold modification, restoration, and functionalization. For large or complex molds, adding metal parts to existing molds is possible, allowing for repairs and the creation of molds with multi-material components, further enhancing overall process efficiency without compromising on hardness or resistance.
For mold manufacturers looking to explore the benefits of additive manufacturing, Prima Additive stands ready to provide tailored solutions to meet specific production needs. We invite companies in the mold sector to contact us to discuss potential collaboration opportunities. Together, we can explore how our innovative technologies can enhance your mold production process, improve efficiency, and embrace cutting-edge manufacturing solutions.
