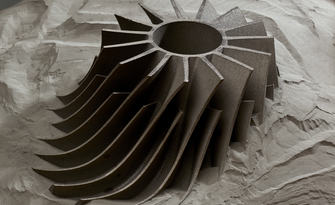
Prima Additive at BIMU 2022 - Made in Italy additive manufacturing becomes more flexible, digitized, and accessible
Prima Additive will be present at the BIMU exhibition in Milan from 12 to 15 October (Hall 15 Stand F32) with solutions that respond to current trends in the manufacturing sector.
Do you want to come and visit us at BIMU?
The world around us is changing, we are increasingly immersed in technological solutions that project us into digitized environments. Similarly, technology solution providers today are faced with the challenge of providing tools that can help digitalize production.
At BIMU Prima Additive will present its vision of digitized production, with important innovations both in terms of products and in terms of services.
From the point of view of the products that will be exhibited at the Prima Additive stand, the main novelty is the IANUS multiprocess robotic cell. This machine, presented as a world premiere at BIMU, is based on a system consisting of an Autonox robotic arm and a laser source, inserted inside a cell that boasts a working volume of 1600 x 1200 x 700 mm.
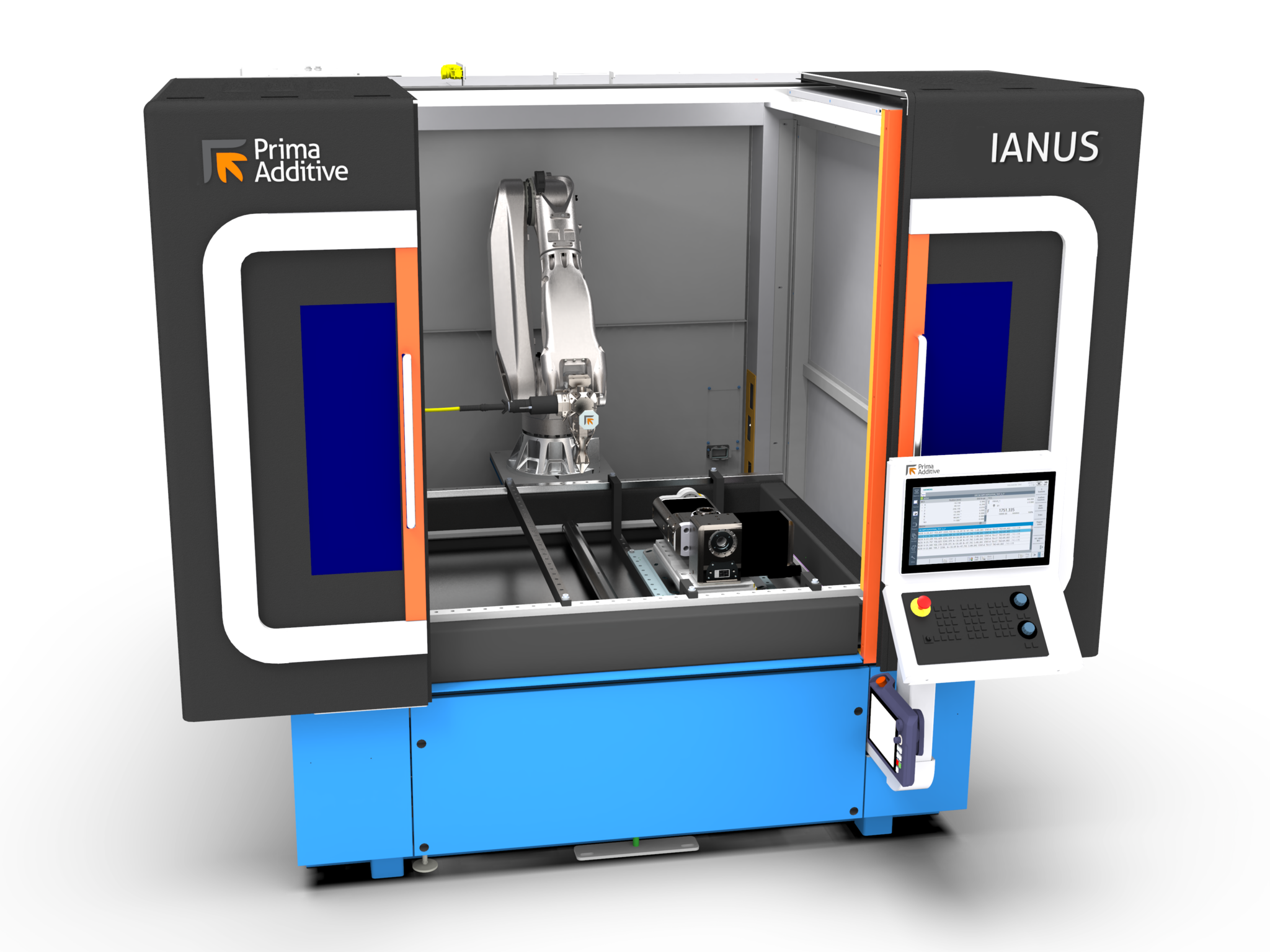
The peculiarity of this cell is the possibility of being configured for different laser processes. The version exhibited at the fair will be equipped with a single laser process, specifically the Direct Energy Deposition based on the use of metal powder for the construction of components from scratch, but also for the repair, coating, and addition of custom parts on metal pieces. Thanks to the flexibility of this machine, however, it is also possible to opt for different laser processes, such as Direct Energy Deposition based on the use of metal wire as a starting material, but also other laser processes not necessarily in the additive manufacturing spectrum, such as remote welding and laser hardening.
The name of this solution comes from the Latin god Ianus, also known as the Italian "Giano", an iconic divinity with two faces. Just as the god Ianus has two faces, the Prima Additive IANUS robotic cell can also be configured to perform two different processes (for example additives and laser hardening) in the same machine, using the same laser source or different laser sources on the same robotic arm. . Thanks to the possibility of installing two dedicated warehouses, it is possible to switch from one application to another simply by changing the head installed on the robotic arm inside the machine itself. The head change, therefore, becomes comparable to a tool change, increasing the flexibility of the system.
This system presents a series of functional solutions for its inclusion in the factory of the future. In fact, it was developed by Prima Additive in collaboration with Siemens, a leading company in automation and digitalization with specific skills in the field of robotics and additive manufacturing. The integration between the technologies of Siemens and those of Prima Additive Srl is expressed, first of all, through the integration of the robotic arm and the CNC, through the Sinumerik Run MyRobot / Direct Control functionality.
Through this functionality, the user of the machine will be able to interface with the robotic cell using a single control console but above all, he will be able to carry out the movement and programming of the robot using typical instructions of a machine tool, thus exempting him from knowing an additional programming language. specific for robots. The integrated use of the CAD-CAM-CNC chain, made possible by the use of the NX platform and the Sinumerik One numerical control, is completed by the integration of digital solutions and data management.
The solution, based on the MindSphere open ecosystem, involves the use of Siemens Apps that allow you to view, manage and optimize production, such as Manage MyMachine, and remote monitoring and control systems, such as Manage MyMachine / Remote. To complete this digital offer, we find some specific applications, able to manage high-frequency data, based on the Industrial Edge for Machine Tools platform from Siemens.
In order to fully exploit the potential of Sinumerik One, the winning choice was to use the Create MyVirtual Machine, a key tool made available by the Siemens digital portfolio. This software is in fact able to generate a real digital twin of the system and has proved to be extremely useful for facilitating the engineering work in the various stages of development and optimization of the machine, also allowing a considerable reduction in time to market.
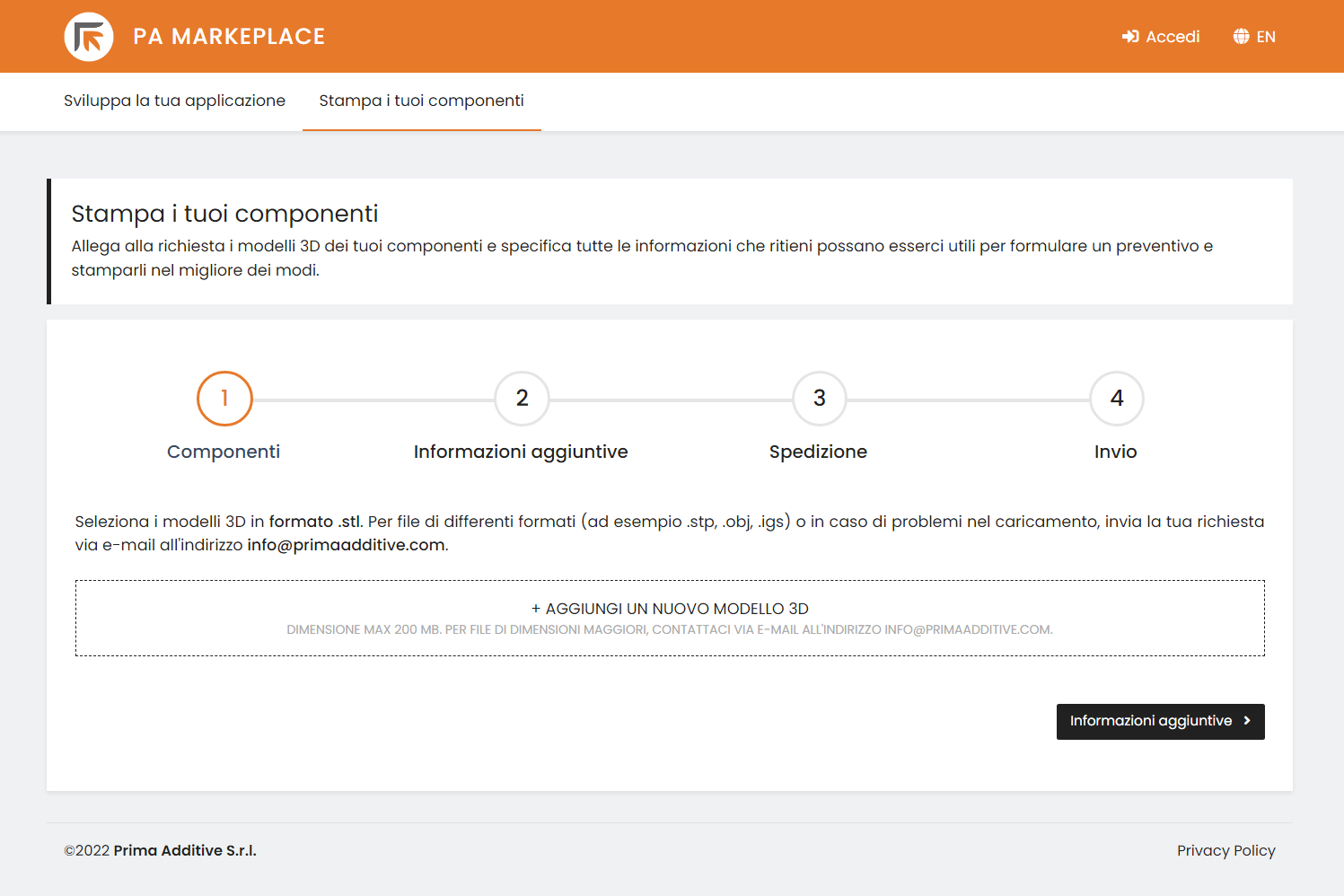
The second big news for Prima Additive will be represented by the launch of the "Prima Additive Marketplace" platform, which represents one of the efforts of the Turin-based company in the direction of reducing the barriers to entry of metal additive manufacturing, at the same time, making production increasingly digitized. Through this platform, accessible at https://marketplace.primaadditive.com and created in collaboration with Morphica, the innovative Italian SME that provides 3D printing services, it will be possible to request the creation of metal components, starting from a file 3D.
The Prima Additive Marketplace leverages the production capacity of Prima Open Additive Labs, the network of companies, universities and research centers that provide support on additive manufacturing, and Prima Additive customers to provide an on-demand production service, which can make the 'additive manufacturing of metal accessible even to companies that do not have the possibility or the volumes necessary to have their own system.
In addition to the possibility of directly requesting the printing of the component, on the platform it is also possible to obtain dedicated consultancy, functional to the realization of an application study, with which to explore the potential of the additive on the specific case of the customer, analyzing the opportunities for engineering of its component and identifying the main advantages and possible criticalities.
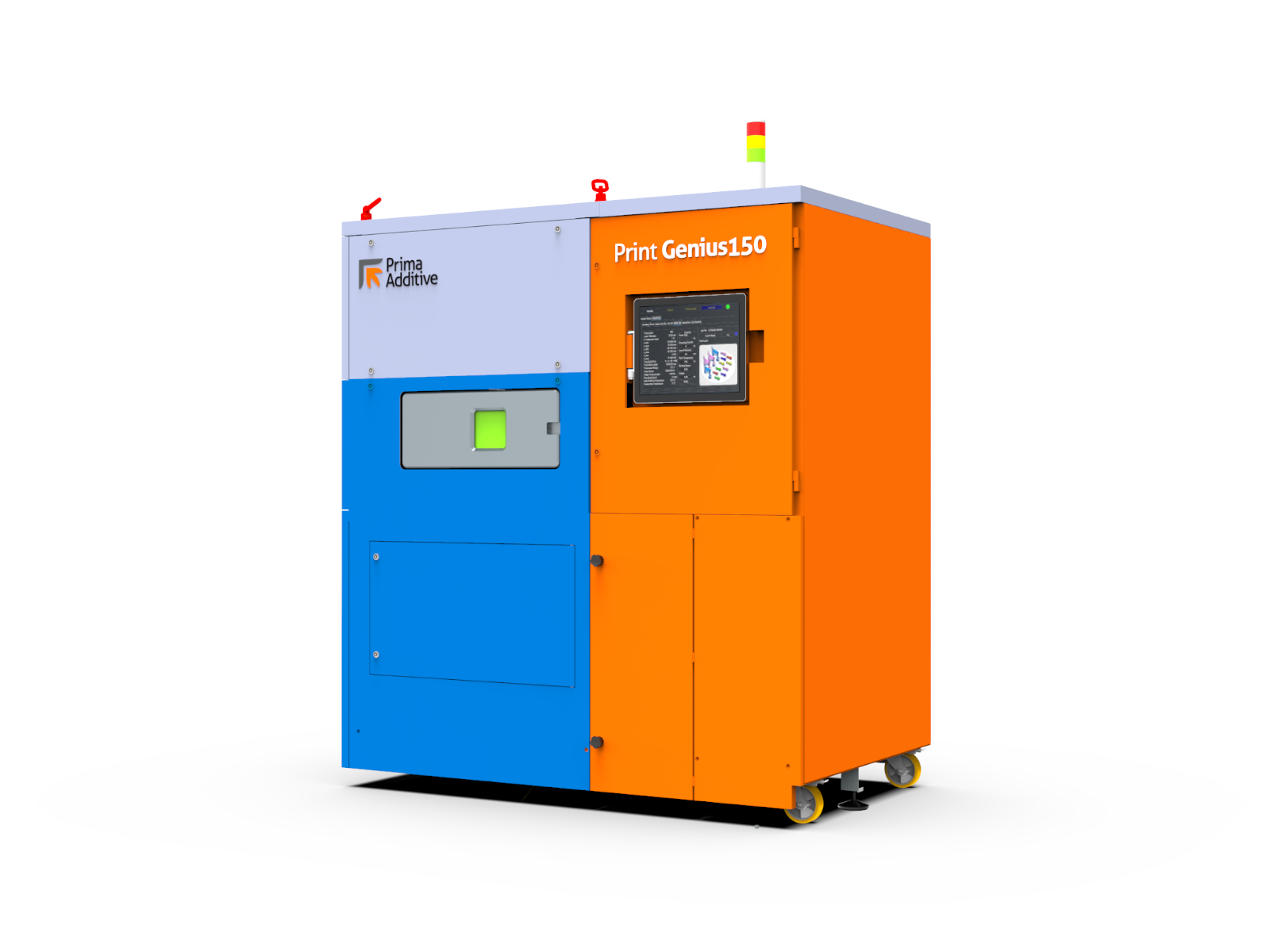
The latest of the solutions exhibited at BIMU is the Print Genius 150, a totally Made in Italy machine that, thanks to the architecture of the laser sources and innovative solutions, allows highly flexible, efficient, smart, and sustainable production.
Print Genius 150, which is part of the line of products with Powder Bed Fusion (PBF) technology, is equipped with two 300W infrared lasers that can work simultaneously in the same work area. With this machine, it is possible to process steel, aluminum, titanium, nickel, chromium-cobalt, and copper alloys with high productivity and quality.
Equipped with a build volume with a diameter of 150 mm and a height of 160 mm, the machine features all the innovations of Prima Additive's PBF solutions, including a system for varying the position of the laser beam focus that optimizes parameters depending on the application, a double preheating system to heat the surface of the powder bed both from above and from below via the heated plate (up to 300 ° C), a high-speed coaxial pyrometer for temperature control in real time and two cameras for process and powder bed monitoring.
Prima Additive's 150 series is Industry 4.0 Ready and allows the integration of monitoring sensors and connection through different standards for IoT functions. The Print Genius 150 integrates, for example, some systems of Materialize, a global provider of software solutions and services for 3D printing, such as the MCP hardware control, for monitoring and control functions in real-time, and the Laser Workload Balancing algorithm, to optimize the workload of the two lasers and maximize the advantage of having two sources on the same machine.
Innovative technologies are not enough to overcome challenges, more and more specialized skills and competences are also needed. For this, Prima Additive offers a very wide range of services, with experts constantly available to provide support and advice.
Do you want to come and visit us at BIMU?
Prima Additive's participation in the BIMU tradeshow is co-financed through the call for proposals "POR FESR 2014/2020 - SC-UP - application code 353 – 49"