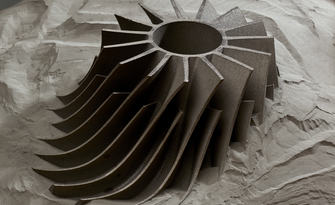
Sustainable Energy Production: The Role of Additive Manufacturing
In today's world, where energy demands continue to soar, the imperative to produce abundant energy with minimal climate impact is crucial. The development of carbon-neutral sources such as wind, solar, geothermal, hydroelectric, and nuclear power marks a significant stride towards this goal. These sources mitigate climate change effects and offer a sustainable alternative to traditional fossil fuels.
Additive Manufacturing plays a transformative role in producing components for sustainable energy generation. As a manufacturing process, Additive Manufacturing is inherently sustainable, minimizing waste by using only necessary material layer by layer to create complex structures. This method contrasts with traditional subtractive manufacturing, where recovery of unused material is not an immediate process. Additive Manufacturing's capability to produce components on-demand further enhances its sustainability, reducing the need for large inventories and long supply chains.
The sustainability of Additive Manufacturing extends beyond its process. It enables cost-effective production of complex parts essential in renewable energy systems, such as intricate turbine blades for windmills or detailed components for solar panels. These parts, often challenging and expensive to manufacture conventionally, can be produced more efficiently with Additive Manufacturing. This is crucial for accelerating renewable energy technologies' adoption, making them more accessible and economically viable.
Additionally, Additive Manufacturing's impact is not limited to renewable energy sectors. In traditional energy industries like oil and gas, Additive Manufacturing offers substantial benefits. By enabling on-site production of components and efficient repair of existing parts through technologies like Direct Energy Deposition, Additive Manufacturing can significantly reduce downtime and operational costs. This aspect is particularly beneficial in offshore platforms or remote drilling sites, where waiting for spare parts can be costly. Furthermore, by repairing and reusing components, Additive Manufacturing contributes to a more circular economy, reducing the environmental impact even in traditionally high-emission sectors.
In conclusion, Additive Manufacturing emerges not just as a tool for production efficiency but as a catalyst for sustainable energy transition. Whether in reducing renewable energy components' costs or enhancing traditional energy sectors' efficiency, Additive Manufacturing stands at the forefront of sustainable industrial innovation. Its role in shaping a greener, more sustainable future for energy production is indisputable, marking a significant step forward in our journey towards environmental stewardship and climate resilience.

Revolutionizing Energy Production with Advanced Additive Technologies
Prima Additive's groundbreaking work in the energy sector showcases the immense potential of Additive Manufacturing technologies. As an industry leader, Prima Additive focuses on two key technological processes: Powder Bed Fusion and Direct Energy Deposition. These technologies are redefining how many components for energy production can be created and maintained, offering significant advantages over traditional manufacturing methods.
Powder Bed Fusion is a sophisticated Additive Manufacturing process utilized by Prima Additive. It involves spreading a thin layer of metal powder and selectively melting it using a laser, based on a digital model. This method is particularly suitable for producing complex geometries and intricate designs that would be challenging or impossible with conventional manufacturing. Powder Bed Fusion excels in creating high-resolution, high-quality parts for any energy application, such as precision components for wind turbines or intricate parts for traditional thermoelectric plants. The key advantage of Powder Bed Fusion lies in its ability to produce lightweight yet strong components, crucial for enhancing the efficiency and performance of renewable energy systems.
Directed Energy Deposition (also known as Laser Metal Deposition), another innovative process employed by Prima Additive, offers immense benefits, especially in repairing and adding material to existing components. Direct Energy Deposition technology works by feeding metal powder or wire into a melt pool created by a laser. This method is particularly effective for repairing high-value components like turbine blades or impellers, extending their service life and reducing waste. The Direct Energy Deposition process is not only cost-effective but also environmentally friendly, as it reduces the need for new raw materials and minimizes waste. Prima Additive's Direct Energy Deposition technology is a game-changer for the energy sector, especially in maintaining and optimizing the performance of existing energy infrastructure.
These advanced technologies from Prima Additive offer numerous advantages over traditional manufacturing methods. They enable faster production times, greater design flexibility, and the production of more durable and efficient components. Additionally, they allow for on-demand manufacturing, which reduces inventory costs and streamlines supply chains

A circular economy approach
One of the most promising and economically viable applications of additive manufacturing in the energy field is the repair of structural components: the option to re-use a worn component, and therefore avoid manufacturing a new one, can save a remarkable amount of resources, reduce costs and create new business opportunities. All of this while fostering sustainability and a model of production that is respectful of the environment, because recycling existing assets rather than producing waste ties in with the core principles of the Circular Economy paradigm. The advantages in the repair of structural components are especially great when the parts to be repaired are large and with high added value.

That is the case of one of our customers, global energy leader Enel – which operates a Prima Additive LASERDYNE® 795 at its power plant in Santa Barbara (Arezzo, Italy) – was able to leverage important benefits by using Direct Energy Deposition (DED) technology. Prima Additive and Enel jointly studied the repair application, selecting a centrifugal impeller used in the geothermal production site. Normally, this component wears down after one year of continuous operation and would require a new one to be manufactured. However, with the LASERDYNE 795 DED system and Prima Additive’s support, Enel successfully qualified the component repair application, putting the repaired impellers back into operation.
The repair strategy began by rectifying the damaged component to create a flat and homogeneous surface, upon which material was added using DED technology to reconstruct the component’s original shape. Prima Additive's application engineers created a replica of the impeller end using Powder Bed Fusion technology to study and test the best deposition strategy. Different manufacturing approaches were evaluated, and it was decided to use 3+2 axes for the component’s positioning. Using a 17-4PH steel alloy, known for its high mechanical strength and resistance to wear, it took 2.5 hours to repair the impeller. Enel then analyzed and certified the outcome, milled the component to restore its original geometry, and plans to continue repairing and reusing these parts, thus contributing to a more circular economy.
Prima Additive and Enel continue to explore new applications of AM technology, aiming to repair components, reduce consumption, costs, and environmental impact, thereby paving the way for new sustainable business models.

Prima Additive invites companies in the energy production sector to explore how these innovative Additive Manufacturing technologies can enhance their business operations. Whether it's through improved efficiency, reduced production costs, or fostering innovation, our team is ready to provide expert advice and tailored solutions. Contact Prima Additive today to discover how our expertise in Additive Manufacturing can benefit your business and help you achieve new heights in the competitive energy sector.
