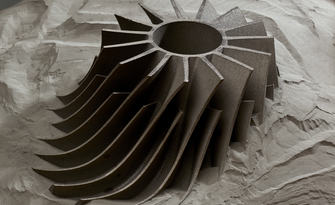
The 2020s, as seen so far, confront the world with some challenges, the solution of which will be of crucial importance for the future. First of all, there is the pandemic situation, which has led each of us to rethink our lives and, more specifically, has led companies to reconsider their priorities: the difficulties in moving and the slowdowns in world production have generated a global supply chain increasingly fragmented and less reliable. Secondly, the cost of raw materials and energy has risen enormously, with a consequent increase in production costs and uncertainties in each market. As a third aspect, probably even more important than the first two, there is the issue of climate change: a phenomenon that is now underway and undeniable, which could generate even greater upheavals than those we have witnessed in the last two years.
Faced with these challenges, all of us as individuals, but especially manufacturing companies, are called to act, looking for a solution to face them and to do their part in their solution, providing our customers with solutions that strengthen their competitiveness, improve their productivity, flexibility, and efficiency.

From Prima Additive's point of view, as suppliers of industrial systems, our role is to provide manufacturers with the right tools to face the uncertainties of these times. Metal additive manufacturing, in fact, offers concrete answers to the three problems mentioned by revolutionizing the approach to the component, from its design to its realization, thus allowing the conception of new business models and participating in making production more sustainable.
First of all, this technology enables the so-called “on-demand manufacturing”: that is the possibility of making complex parts in metal, producing only what is needed, when it is needed, and where it is needed. By doing so, it is possible to reduce warehouse availability, reducing the impact it has on consumption and operating costs. Furthermore, consumption and logistics costs are reduced to transport the pieces from one area of the world to another. Finally, the supply chain is optimized, protecting it from any type of slowdown generated by a global supply chain that now is more fragmented and less and less reliable. By internalizing the production of many pieces thanks to additive manufacturing, the re-shoring of your production, therefore, becomes simple, and the number of steps required to create the finished piece is reduced.
From the point of view of reducing material waste, as well as the growing difficulty in finding raw materials and their constantly growing cost, additive manufacturing is a great ally since it allows you to limit the use of the material to the quantity necessary for making the piece. The metal powders used in the additive process can then be recycled, allowing a favorable and more sustainable approach to waste reduction than the removal process which involves a large percentage of waste and a long process of recovering it. The recycling of unused powders in the additive process takes place instantly and autonomously, with the possibility of reusing the powders for different production cycles.
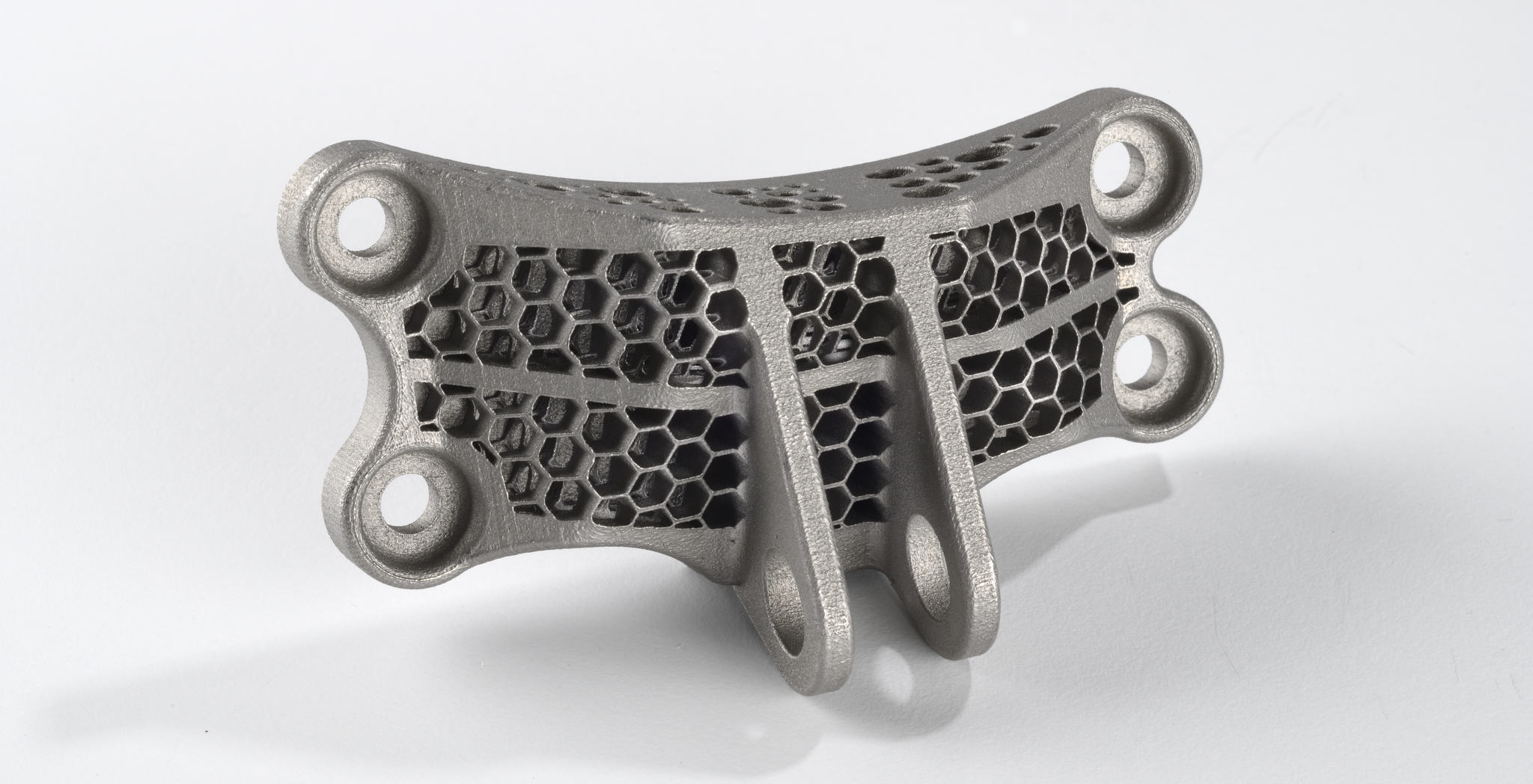
The sustainability of Additive Manufacturing is also highlighted in the product, which can be made with optimized geometries, making it lighter, with the same functionality and mechanical characteristics.
This is also possible because additive manufacturing is not limited to the production phase of a component, but reaches its maximum potential when it involves thinking about what comes before and what comes after production, that is, design and disposal. First of all, the great opportunities offered by this technology pave the way for new frontiers in the field of design: an efficient design of a part not only considers its production and use but also what will happen when it has to be disposed of. Having such a versatile technology helps to reduce assemblies, but also the number of different materials used: in this way, when the component reaches the end of its life cycle, it will be easier to recycle it. Furthermore, the pieces designed considering their use are “green” in the effects they can generate during their use. Speaking of a sector that was the first to believe in this technology such as aerospace, for example, the adoption of additive-made parts is not only an advantage in terms of aircraft functionality, but also represents a real element of respect for the environment and sustainability of the aerospace business. Reducing the weight of an aircraft allows at the same time to reduce the fuel consumption of the aircraft and, consequently, reduce its CO2 emissions into the atmosphere. The same is true for the automotive industry, where the electrification of vehicles leads to increasingly heavier vehicles: the challenge of the next few years will lie in their lightening to increase their efficiency and, we are sure, the additive will play a crucial role in this challenge.
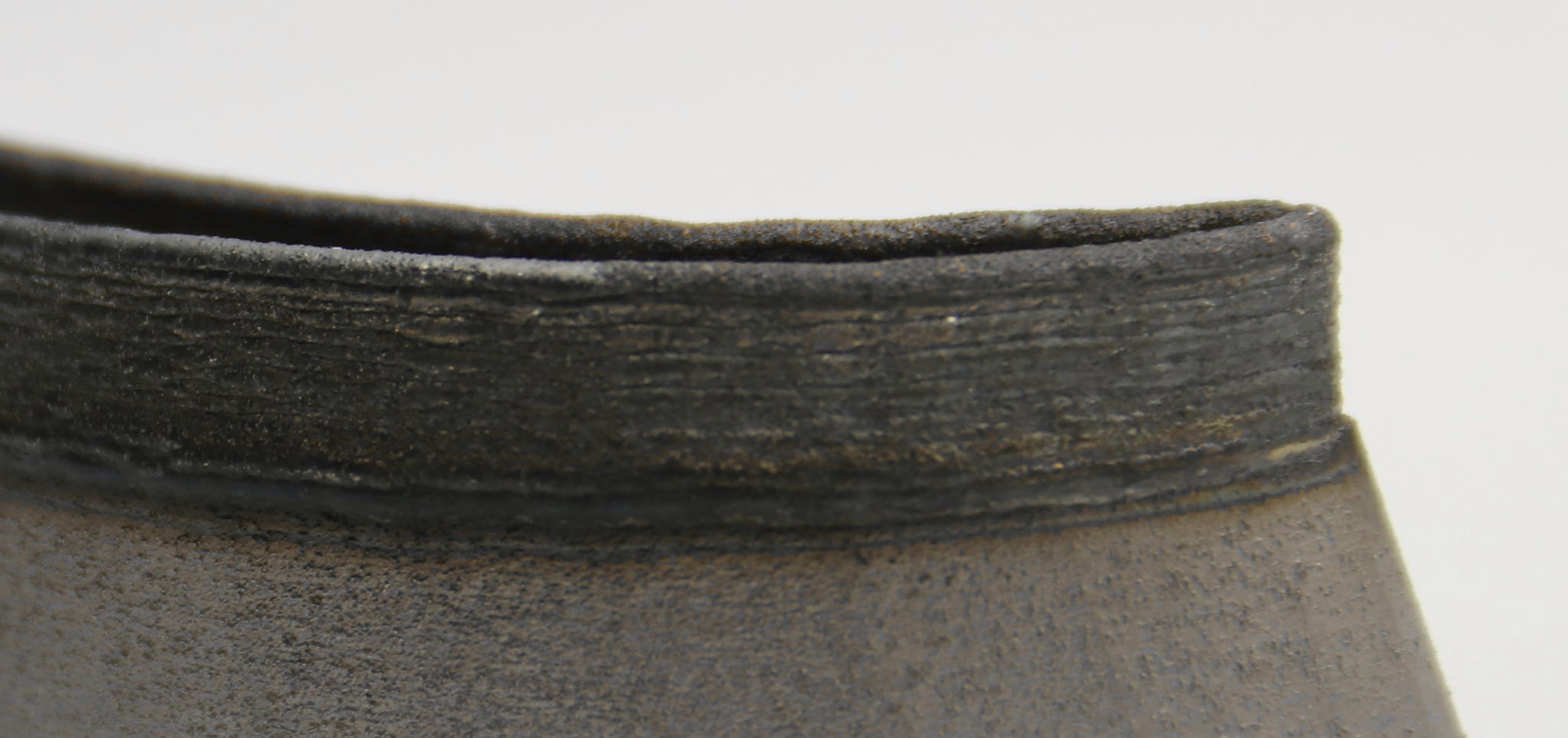
In addition to lightening the products, it is important to work on concepts of functionalization of the components or their repair. With this in mind, Prima Additive not only provides solutions with Powder Bed Fusion technology, useful for producing finished parts but is also active with Direct Energy Deposition technology, proposing systems that fit perfectly within an idea of industrial sustainability and circular economy, allowing to repair or functionalize metal parts: a component, when it is too worn, can be repaired in a few hours, thus extending its life cycle and avoiding further use of resources and energy to create a new one.
All these themes show how metal additive manufacturing can actively contribute to a more sustainable approach and Prima Additive's goal of making this technology increasingly competitive, to allow the end user to adopt a profitable solution to face the challenges of our times.
This goal is pursued by Prima Additive through the creation of new system concepts, the development of a reliable process for different applications and materials, and the full support to the customer to adopt this technology. This is also possible because Prima Additive is part of the Prima Industrie Group, which has a history of technological innovation in the industrial manufacturing sector. Our DNA as innovators in the field of mechatronics, photonics, and process innovation will allow us to create ever more performing, more productive, and more automated systems, with the aim of satisfying the needs of our customers and supporting them in an environment which is increasingly interconnected, agile, and dynamic.