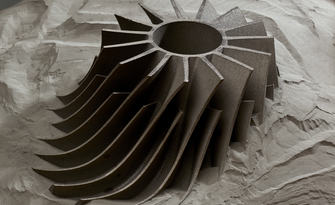
Advancing Tooling Efficiency with Additive Manufacturing
Tooling has always been a significant cost center for many manufacturing companies, often constraining production flexibility and the incorporation of design modifications. In effect, traditional tooling methods, while established, grapple with substantial cost implications and rigidity in production processes, making design alterations both expensive and challenging.
The emergence of Additive Manufacturing has heralded a paradigm shift in tooling methodologies. This technology, distinguished by its layer-by-layer construction through digital processes, excels in circumventing the limitations inherent in traditional techniques. Additive Manufacturing offers the capability to produce custom tooling faster, at reduced costs, and with unprecedented design flexibility.
One of the primary challenges in conventional tooling is the prolonged production time and the high costs associated with mold fabrication. Additive Manufacturing streamlines this process, enabling the creation of intricate and complex tool designs that would be impractical or impossible with conventional methods. This innovation not only reduces production time but also significantly cuts down on material wastage.
Furthermore, Additive Manufacturing introduces a level of customization in tooling that traditional methods cannot match. The ability to rapidly prototype and iterate designs allows for more agile responses to market demands and design changes. This agility translates into a more dynamic production environment, where adapting to customer needs and evolving designs becomes a seamless process.
The cost-benefit ratio also heavily favors Additive Manufacturing. Traditional tooling often requires significant upfront investment in molds and machinery, which becomes economically burdensome, especially for small batch productions or bespoke items. In contrast, Additive Manufacturing's digital nature means that changes can be made quickly and efficiently without incurring additional costs for new molds or tooling adjustments.
Moreover, the improved material efficiency and waste reduction inherent in additive manufacturing contribute to a more sustainable production model. This aligns with the growing global emphasis on environmentally friendly manufacturing practices, adding another layer of appeal to this innovative approach.
These are the reasons why Additive Manufacturing in tooling is not just an alternative; it's a superior method, offering cost savings, flexibility, speed, and sustainability. For companies looking to stay competitive in a rapidly evolving manufacturing landscape, embracing this technology is not just advantageous; it's essential.
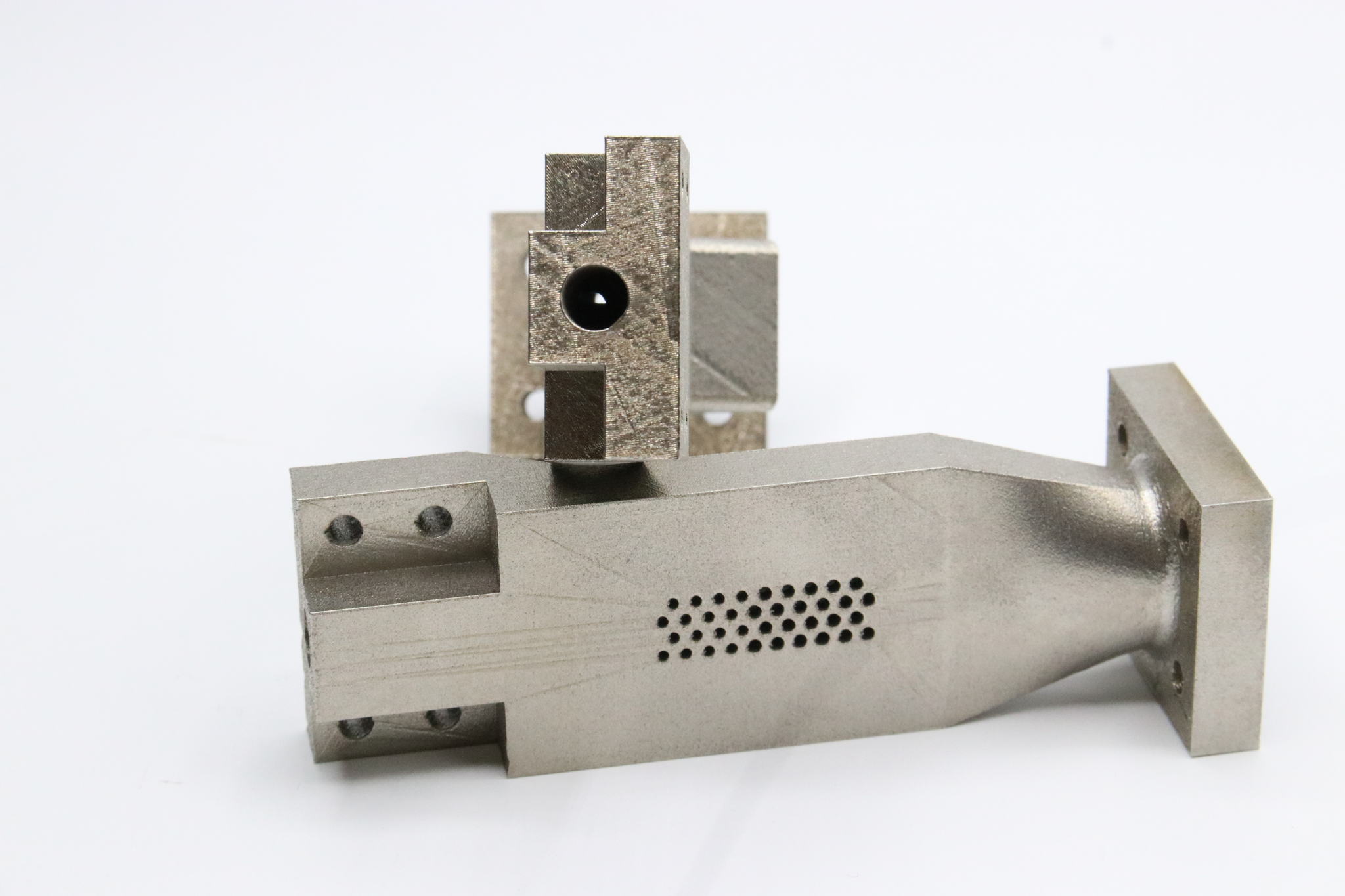
Additive Manufacturing for Tooling: Innovations and Applications
We recognize that Additive Manufacturing's design freedom, efficiency in manufacturing complex geometries, material savings, and overall cost-effectiveness are key to advancing tooling in various industries, especially, but not only, automotive.
Prima Additive's expertise in Additive Manufacturing for tooling offers solutions that are not just alternatives to traditional methods but are superior in many ways. Our approach to tooling is characterized by rapid prototype tooling, customized mold design, and the creation of high-efficiency tooling that leverages the unique advantages of Additive Manufacturing. These capabilities enable the production of tools that meet the high demands of modern manufacturing processes, like those involved in hot stamping and injection molding.
Moreover, Prima Additive's tooling solutions prioritize sustainability. The company's commitment to reducing vehicle weight, as seen in the automotive sector, aligns with global efforts to minimize environmental impact. This commitment extends to various industries where Additive Manufacturing can play a critical role in developing more sustainable manufacturing practices.
In a sector such as the automotive one, additive manufacturing can be used for applications relating to the creation of body panels and structural components. In fact, using AM, tools for deep drawing and stamping processes can be created with complex cooling channels that improve temperature management and reduce cycle times, ultimately enhancing the structural integrity and quality of the final product.
The healthcare industry, particularly orthopedics and dental sectors, benefits greatly from additive technologies. These methods are used to produce customized surgical tools and dental fixtures tailored to individual patient anatomy. The ability to create patient-specific tooling directly from medical imaging data not only speeds up the surgical process but also increases the precision and effectiveness of medical procedures.
In the energy sector, particularly oil and gas, tooling often requires materials that can withstand extreme environments and pressures. Metal AM can produce parts that meet these harsh operational demands with materials like Inconel and stainless steel. Tools such as drill bits, impellers, and turbine blades are manufactured using AM to have internal structures that optimize their strength-to-weight ratios and enhance their functional performance in challenging conditions.
The rapidly changing consumer electronics industry utilizes metal AM to develop molds for plastic casing and other components that need to be developed quickly to stay ahead of market trends. The ability to rapidly prototype tooling for mass production allows companies to test designs without significant investment in traditional tooling, which can be costly and time-consuming. This rapid prototyping capability enables faster product launches and the flexibility to respond to consumer demands with agility.
The integration of Additive Manufacturing into tooling also brings about a significant reduction in production times and costs, as Prima Additive's advanced machines facilitate a swift transition from design to final result. This agility is crucial in today's fast-paced market, where the ability to quickly adapt and innovate is paramount.
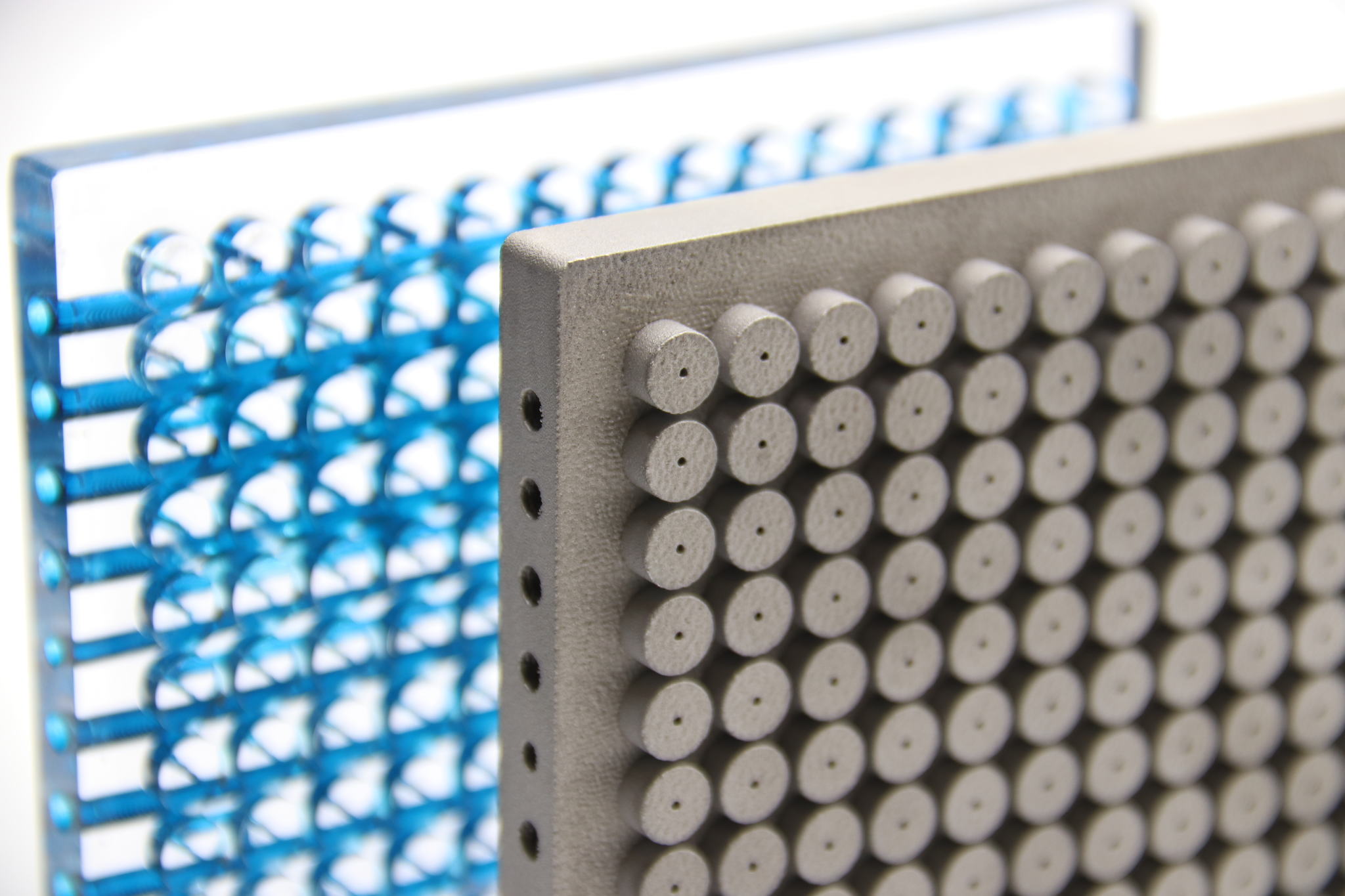
A Partnership Approach to Additive Manufacturing for Tooling
At Prima Additive, we understand that the journey into Additive Manufacturing for tooling extends far beyond the mere acquisition of machinery. It's about forging a partnership that guides and supports our clients at every step. This philosophy is deeply embedded in our approach to customer service, as we don't just sell machines; we offer a partnership built on trust, expertise, and a commitment to your success.
Our commitment to customer support is evident in our comprehensive services. Prima Additive's international team of qualified technicians is equipped to provide detailed technical analyses and effective solutions remotely, ensuring that wherever you are, we are with you, supporting your business.
Our approach to additive manufacturing is holistic, emphasizing the importance of walking alongside our customers through every step of the process. From the initial case analysis, simulation of printing strategies, and reporting on convenience and sustainability, to the evaluation of processes and materials, prototype production, and advanced training, our experts are there to guide you.
For businesses looking to explore the possibilities of Additive Manufacturing in tooling, we extend an invitation to connect with us. Experience the Prima Additive difference, where partnership, expertise, and innovation come together to redefine what's possible in manufacturing. Contact us today to begin your journey into the future of tooling with a partner you can trust.
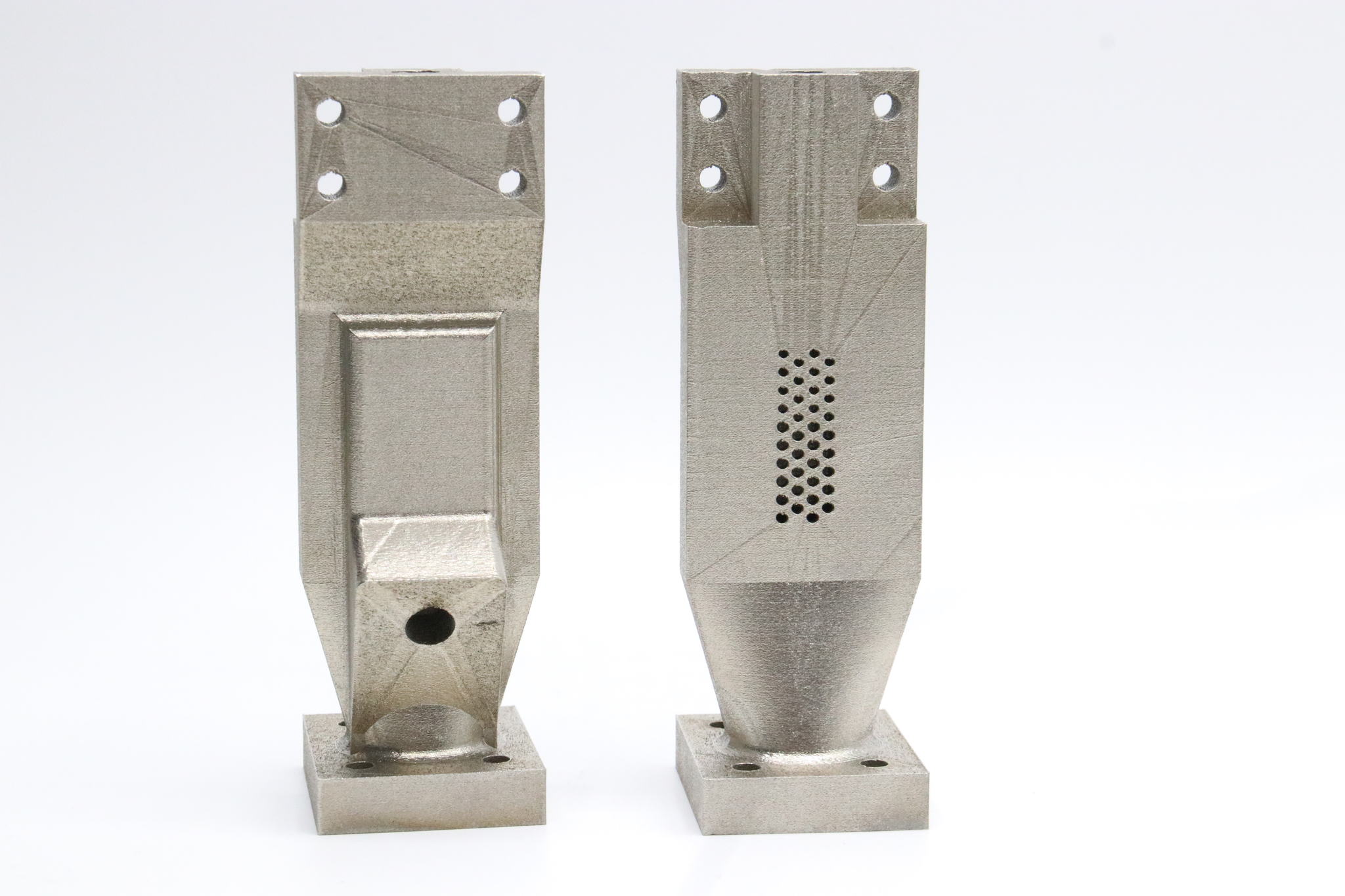