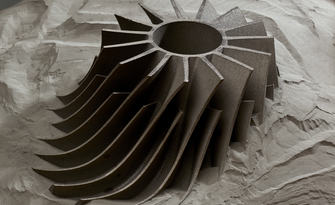
Enhancing Production with Multi-Laser Additive Manufacturing
What is Multi-Laser Additive Manufacturing? We can define the Multi-Laser Additive Manufacturing technology by many different points of view, but first of all we can say that it is a transformative approach in the field of industrial 3D printing. This innovative process employs multiple laser sources in Powder Bed Fusion, a technique where a laser selectively melts powdered material to create high-precision components layer by layer. The integration of multiple lasers allows you to work on multiple areas of the platform at the same time, thus significantly reducing construction time and improving productivity. It's not just an incremental improvement—it's an essential element when you need more efficiency and productivity.
At Prima Additive, our dedication to innovation has led us to a comprehensive exploration of Multi-Laser Additive Manufacturing capabilities. We believe in the importance of developing new technologies, and thanks to our expertise in laser material processing we can offer our customers unparalleled production solutions. Our research and development team has spent countless hours testing and refining our Multi-Laser Additive Manufacturing processes to ensure they meet the high standards of quality and reliability that our customers expect.
The economic advantages of Multi-Laser AM are substantial and multifaceted. By employing multiple lasers, there is a direct correlation between the number of lasers and the increase in build rate, leading to shorter production times and higher throughput. This efficiency gain translates directly into cost savings, particularly for large-scale production runs where the time saved accumulates rapidly. Additionally, the flexibility offered by Multi-Laser Additive Manufacturing means that manufacturers can adapt quickly to changing production demands without sacrificing quality or efficiency.

Moreover, the ability to work on multiple parts concurrently or to work with multiple lasers on a single large part with intricate details offers a flexible production approach that can be tailored to specific economic goals. This adaptability is crucial in a market where customization and rapid turnaround times are increasingly demanded. Many studies show that the economic benefits of this approach to laser metal Additive Manufacturing extend beyond mere production speed, expanding on other aspects such as, for example, lower energy consumption.
In the context of Prima Additive's operations, Multi-Laser Additive Manufacturing has allowed us to offer solutions that allow our customers to have a competitive pricing while maintaining the high quality of their products. This technology has been a game-changer for our customers, particularly in industries where precision and speed are paramount. Our Multi-Laser systems have been instrumental in producing components for aerospace, automotive, and medical industries, where the margin for error is negligible, and the cost of failure is high.
In conclusion, we can say that Multi-Laser AM is not just a technological advancement; it's a strategic economic asset. It represents a leap forward in manufacturing capabilities, offering unprecedented levels of efficiency and flexibility. At Prima Additive, we are committed to harnessing the full potential of this technology to provide our clients with the best possible solutions for their manufacturing needs.

Precision and Challenges in Multi-Laser Additive Manufacturing
The production quality in Multi-Laser Additive Manufacturing systems is influenced by a myriad of technical parameters. According to the most comprehensive analyses available factors such as laser power, scan speed, and layer thickness are pivotal. Each parameter must be meticulously controlled to ensure that the multiple lasers work harmoniously. For instance, laser power must be sufficient to ensure proper melting of particles, while scan speed must be adjusted to maintain the thermal stability of the material. Layer thickness must be calibrated to balance between resolution and build speed, a delicate equilibrium that is crucial for the integrity of the final product.
Moreover, the overlapping region role in Multi-Laser AM appears to be crucial. The overlapping region is where the paths of multiple lasers intersect or cover the same area of the build platform. This region presents both challenges and opportunities. Mismanagement of this critical zone can lead to defects such as porosity or lack of fusion, while proper control can significantly enhance build quality. For example, when two lasers operate in close proximity, their thermal influences can interact in ways that may affect the microstructure and mechanical properties of the final part. Therefore, understanding and controlling the thermal gradient in the overlapping region is essential for ensuring consistent quality across the entire build.
A well-designed scanning strategy can mitigate the risks associated with overlapping laser paths and can significantly improve the surface finish and mechanical properties of the final product. By optimizing the sequence and orientation of the laser scans, manufacturers can reduce the occurrence of residual stresses and deformations.
Prima Additive's multi-laser solutions are designed so that all lasers can work on the entire work area, according to a full overlap concept: for this reason, optimizing the overlapping strategies is crucial for achieving the full potential of Multi-Laser Additive Manufacturing. By carefully coordinating the timing and positioning of each laser, it is possible to minimize the potential negative effects of overlap. This requires sophisticated software algorithms that can predict and compensate for the complex thermal interactions that occur during the build process. For this reason, we have developed an algorithm together with Materialise, able to perfectly manage the work of lasers working simultaneously, optimizing load balancing to always have the best possible use of laser sources and, above all, to avoid non-productive times, optimally managing the workload of the lasers involved in the process. By doing so, our customers can produce more quickly parts with uniform mechanical properties and minimal internal stresses.

Optimizing Multi-Laser Additive Manufacturing
The decision between investing in a single multi-laser system versus several single-laser systems hinges on a thorough analysis of production needs. It's not a one-size-fits-all solution; each manufacturing scenario demands a tailored approach.
At Prima Additive, we have embraced the multi-laser paradigm wholeheartedly. Our state-of-the-art systems are equipped with up to four lasers that can operate simultaneously on the same build area. This capability not only reduces production times but also enhances the detail and precision of the parts produced. Our full overlapping laser technology ensures that there is uniform coverage across the entire build area, which is essential for producing parts with consistent mechanical properties. We have invested in advanced software that controls the laser paths with precision, ensuring that the overlap regions are managed effectively to produce the highest quality parts.
In addition, we do not only provide solutions equipped with infrared lasers, but also offer the possibility of equipping machines with Powder Bed Fusion technology with green lasers, which with their short wavelength (532 nm) are particularly efficient in the processing of highly reflective alloys. Thanks to our configuration possibilities, it is possible to install multi-laser solutions on our machine platforms that involve only infrared lasers, only green lasers or both types of sources, as in the case of the Print Genius 150 Double Wavelength, equipped with an IR and a green laser in the same system, able to work alternately for maximum precision on each material.
We at Prima Additive understand the intricacies of Multi-Laser Additive Manufacturing and are dedicated to helping businesses harness its full potential. We encourage companies to reach out to us to discuss how this technology can revolutionize their production capabilities. Our team of experts is ready to provide specialized consultation to determine if this technology is the right fit for your products. Let's explore the possibilities together and take your manufacturing process to the next level.