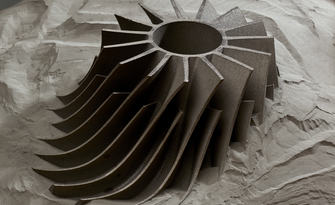
Inert chamber

Direct Energy Deposition technology
Processes titanium and other reactive materials to the highest quality
Direct Energy Deposition technology
The system consists of a sealed main cabin (6 sides, including floor) enclosing the machine, connected to an antechamber for loading/unloading the part, keeping the inside of the main chamber inert.
Thanks to the automated system for moving the rotary table from the working position to the loading/unloading position inside the antechamber, use of gloves from the outside to remove the part from the worktable is not required.
To allow the roto-tilt table to be moved and to separate the two chambers, the system is equipped with an automatic internal door, so that the inertisation process only needs to be carried out in the antechamber after the part has been loaded/unloaded.
The door can only be opened when the oxygen level is sufficient. Rapid transition from inert atmosphere to safe loading/unloading conditions by forced air intake.
The gas management system in both chambers makes it possible to keep the oxygen percentage below 100ppm, but achieve oxygen concentration values below 50ppm can also be achieved. This system saves on the amount of inert gas used for inertisation as new gas (from the supply cylinders) is only used for the first purging phase.
Direct Energy Deposition technology
Direct Energy Deposition technology
Direct Energy Deposition Technology
Direct Energy Deposition technology
Application support
Open innovation
Circular economy inspired
© Prima Additive S.r.l. | Corso Re Umberto, 54 - 10128 Torino (TO) Italia | Share Capital € 116.860,77 fully paid up | VAT 11434740012 - C.C.I.A.A.Torino 1213183 | Reg. Impr. Torino n. 11434740012