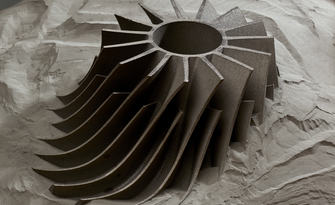
300 Family
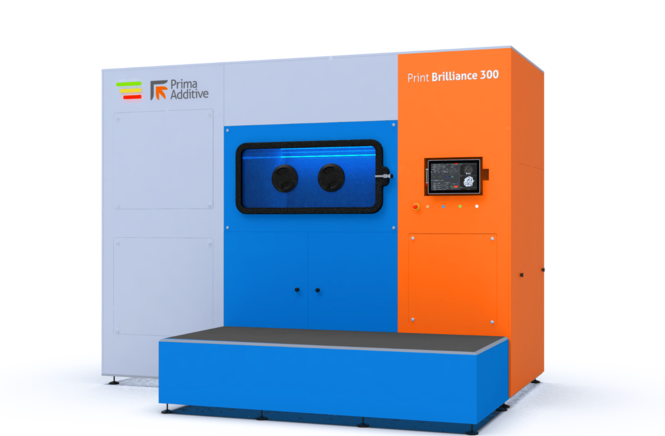
Powder Bed Fusion Technology
High productivity and precision for medium and big-sized components manufacturing.
PRODUCTIVE
Up to four lasers working simultaneously during the execution of the same job over the entire building platform area (100% overlap) according to different strategies such as: quality mode, and production mode.
FLEXIBLE
Possibility of reducing the working chamber to meet customer needs.
EASY TO SET UP
Different powder handling options: Manual (refillable hopper), Semi-automatic (pneumatic conveyor), or Automatic (closed loop from the sieving unit to the machine in inert conditions).
EFFICIENT
Optimized gas filtering unit for minimum nitrogen or argon consumption with a system of backflushing that improves the filter cartridges' lifetime reducing the number of changes and the time to replace them.
The Print 300 Family is a series of machines with a working volume of 330x330x400 mm, available in three different laser configurations:
- Print Sharp 300 single laser
- Print Genius 300 dual laser
- Print Brilliance 300 quad laser
Equipped with an automatic chamber extraction system that allows removal at the end of the job of the entire working chamber with the printed part and the remaining powder to accelerate the set-up activities for a new job, improving the production rate.
The ideal solution for highly productive applications.
The system is equipped with an automatic working chamber extraction system, which allows to remove at the end of the job the entire working chamber with the component and the remaining powder inside, to speed up the set-up activities for a new job, increasing the overall productivity of the system and allowing depowdering activities to be carried out in an external system.
It is possible, on request, to reduce the production area of the system according to the customer's needs.
There are several options for powder handling:
- Manual: the machine is equipped with a hopper filled manually by the operator, which automatically feeds the machine to complete an entire job
- Semi-automatic: the powder is inserted into the system thanks to a pneumatic conveyor that automatically collects the powder from an external hopper that can be filled manually, which can have customized dimensions according to production needs
- Automatic: the system is fed with a pneumatic conveyor that collects the powder from a hopper fed in a closed loop and in an inert atmosphere by another independent pneumatic conveyor that recovers the powder directly from the sieve
The machine, in its multilaser version, can operate with all laser sources simultaneously during the print job, with the lasers working on the same work area according to two possible strategies that can be set by the user: quality mode and production mode.
Bidirectional recoating.
The laser sources are air-cooled, therefore they do not require any additional external units.
Open parameters, suitable for carrying out research and development activities on the process and on materials.
The filter unit is optimized to consume as little nitrogen or argon as possible, with a filter cartridge system that reduces the number of filter changes and the time required to change each cartridge (about 10 minutes each) to meet production needs. and those of the 4 lasers without compromising print quality, thanks also to the cyclonic system that prevents dust residues from ending up in the cartridges. The filter unit also has an automatic backflushing function, which allows you to unclog the filter cores during the process, in order not to interrupt printing. The filter unit includes automatic passivation of the filter cartridge to eliminate any safety issues when replacing the filter cartridge.
- Building volume: 330 x 330 x 400 mm
- Build rate: 15-120 cm3/h (depending on material used and part geometry)
- Deposition layer thickness: 0.02 – 0.1mm
- Layer width: 0.1mm (single track width)
- Laser power (Print Sharp 300): 500 W IR single mode
- Laser power (Print Genius 300): 2 x 500 W IR single mode (100% Overlap)
- Laser power (Print Brilliance 300): 4 x 500 W IR single mode (100% Overlap)
Materials
Stainless steel, maraging steel, high-temperature nickel alloy (Inconel), titanium alloy, cobalt chrome alloy, aluminum alloy, high strength steel, copper alloy.
Prima Additive helps you choose the right material for each application
Prima Additive recommends and offers a wide range of metallic powders, tested to ensure product quality and repeatable mechanical properties. The process parameters were fine-tuned to the specifications and behavior of the powders during printing, enabling excellent (re)production of the components. Thanks to its portfolio of services, Prima Additive can provide support to customers to evaluate and select the most suitable powder for their applications and needs.
Discover all the materials you can process with our PBF machines
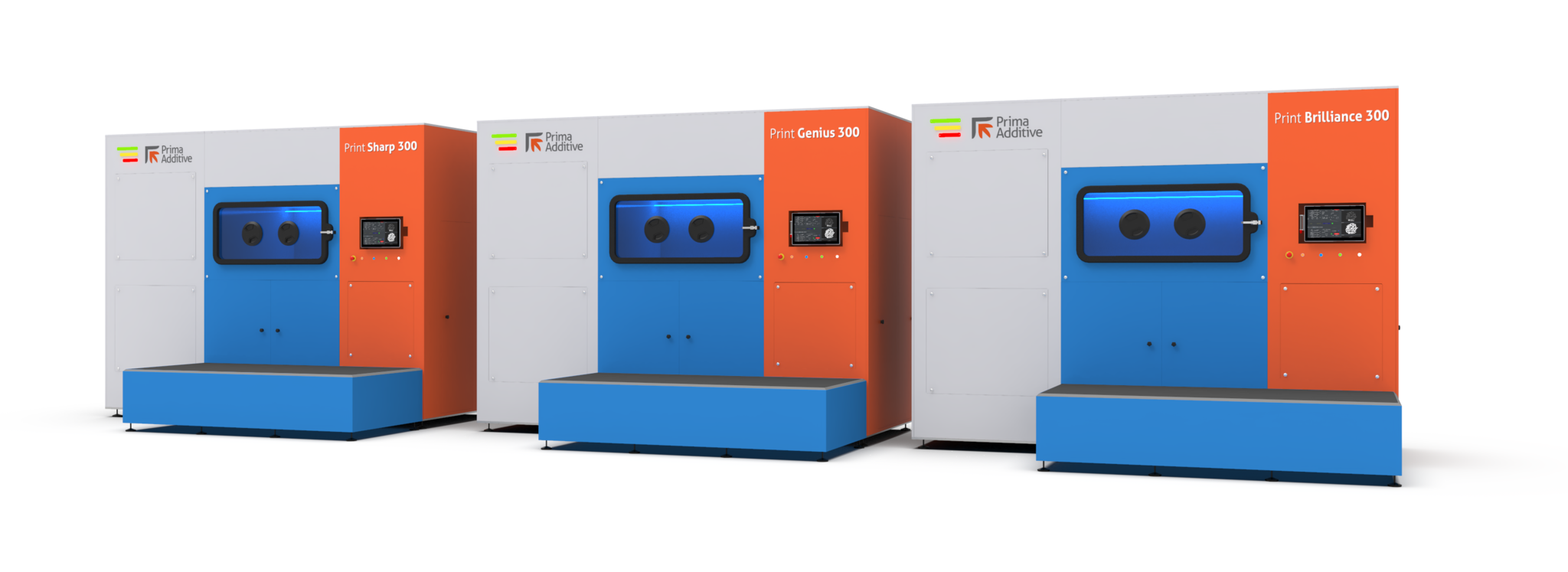
Optimize your Prima Additive machine
Software for PBF
Software for Powder Bed Fusion technology
All the support you need to prepare files for producing additive manufacturing parts.
Green Laser for PBF
Powder Bed Fusion technology
Green Laser for Powder Bed Fusion Technology.
Take advantage of our services
Application support
Transforming ideas into industrial reality
Metal Additive Manufacturing offers limitless opportunities for innovation, but successfully integrating it into an industrial workflow requires the right expertise and support.
Design support
Redefining design for performance and efficiency
The true power of metal additive manufacturing (AM) lies in its ability to create complex geometries that were once impossible with traditional methods.
Request an application assessment
Feasibility assessment
Let's break down the barriers to entry for Additive Manufacturing!
Book a demo
Request a machine demo
Choose between a physical or virtual demo.
Experience the power of additive manufacturing with Prima Additive. Book a demo and explore our cutting-edge solutions for industrial metal 3D printing. Our demo service is available to show you how our technologies can be adapted to your production needs.
Contact us today and try it!
See other products and choose the best solution for your business
Print Genius 150
Powder Bed Fusion Technology
Great versatility thanks to multi-laser technology.
Print Green 150
Powder Bed Fusion Technology
Equipped with a green laser for processing pure copper, copper alloys and highly reflective materials.
Print Sharp 150
Powder Bed Fusion Technology
Designed for R&D applications, for processing steel, aluminum, nickel, titanium, and cobalt chrome alloys.
Print Genius 400
Powder Bed Fusion Technology